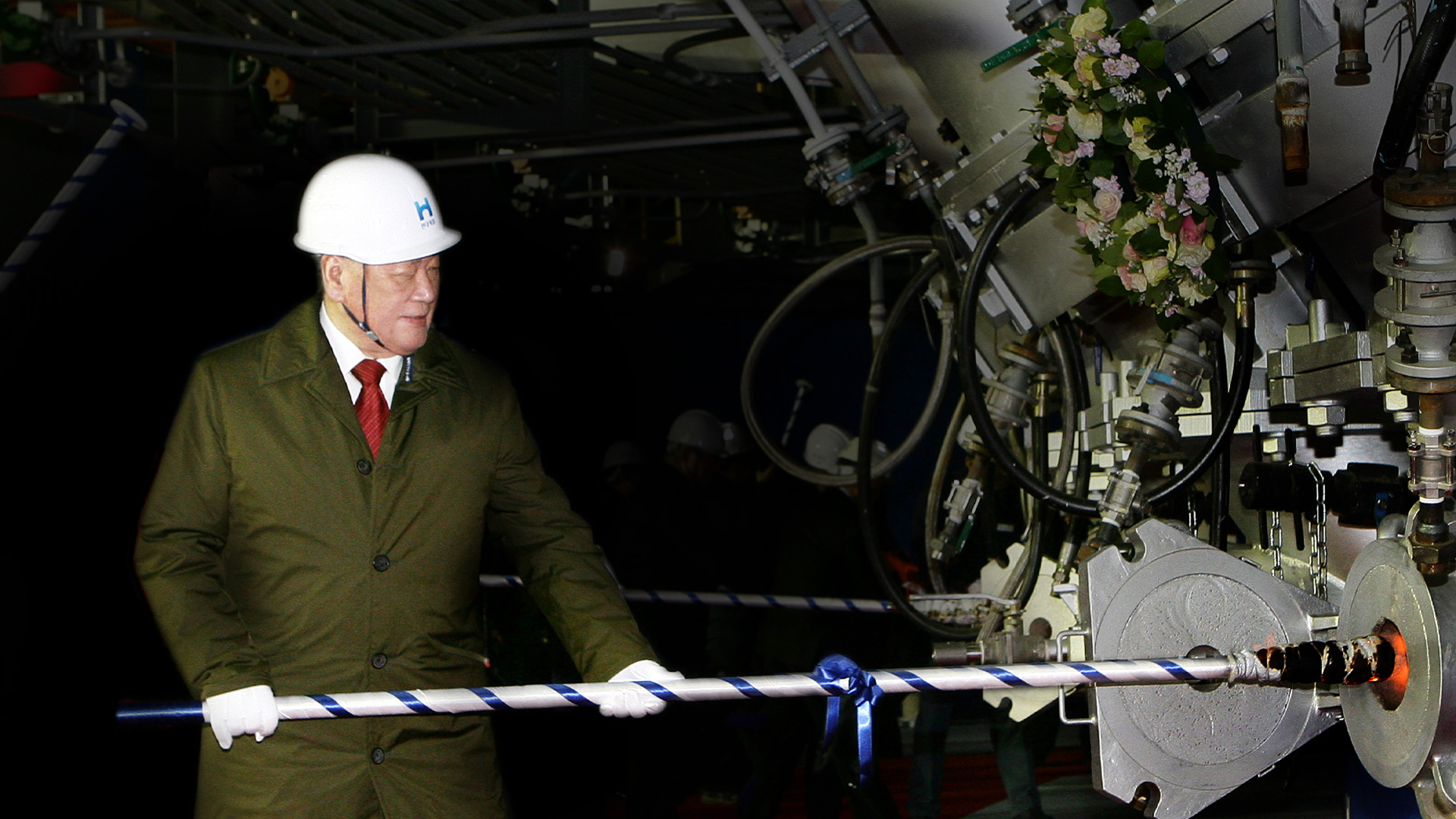
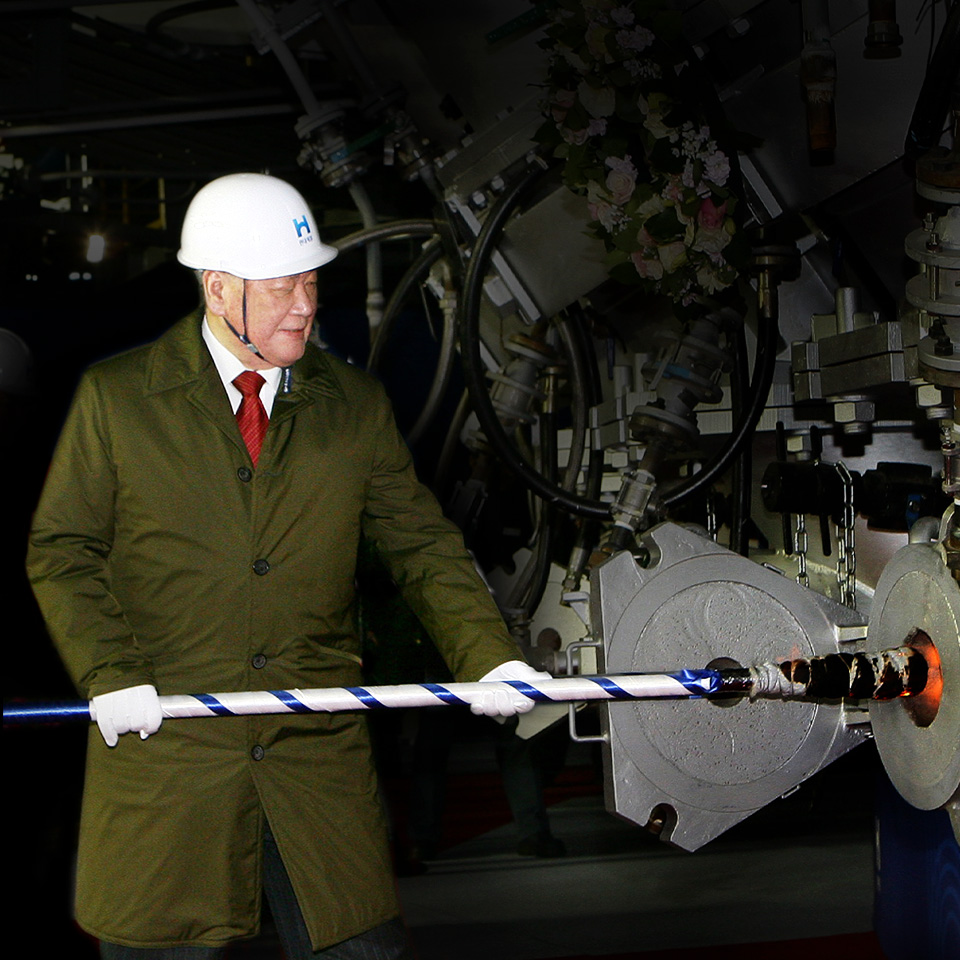
2021.11.12 2005-2010
In 2005, HMG announced Brand Management Vison to become a global top brand. The 2005 was the first year for Global Management and gave shape to the plan with the aim of securing the world’s fifth-highest quality in 2005 and becoming one of the global top five automakers in 2010.
HMG established the first overseas plant with a production capacity of 100,000 units in Turkey (HAOS) in 1997. The Group also started production in the U.S. (HMMA) in 2005 and then rolled up its sleeve for a global management system. In 2006, a Czech plant (HMMC), a second plant in China (BHMC), and a second plant in India (HMI) were consecutively built at emerging markets in Europe and Asia, stepping up globalization.
While outstanding technologies were required to jump over the high walls of going global, gaining support and loyalty from users were more important. With ‘Quality First’ in mind, HMG focused on increasing production in overseas plants to reach customers by manufacturing vehicles that met each customer’s needs. Whenever a crisis emerged, the Group always surprised customers by thinking outside the box in marketing such as the Hyundai Assurance Program.
The Hyundai Assurance Program
The Hyundai Assurance Program was implemented at a time when the demand for vehicles plunged in the 2008 global financial crisis: Hyundai provided a complimentary vehicle return program when customers experienced an involuntary loss of income and health issues within 12 months of purchase date. It was part of an effort to share the difficulties of customers who were anxious due to the economic downturn. The program was an innovative and localized service.
A spirit of challenge in HMG led to a ‘Modularity’ project. What’s important was to lower the failure rate to satisfy customers as the order volumes go up, and inventory management was also important to ease the burden of production costs. As the first modular facilities were constructed in HMMA in 2004, all plants eventually adopted the modular process which supplied components intensively. This translated into upgrading the quality .
Modularity
Modularity is about combining tens of thousands of individual auto components into one large assembly unit. It is a system in which Hyundai MOBIS builds a module by bundling several components, and Hyundai and Kia assemble them and produce automobiles. Modularity contributed to simplify the process from 20,000~ 30,000 components to six to seven modules such as a chassis, a driver's seat, a door, and a seat, enhancing the quality accordingly. Modularity played a pivotal role for HMG to become world's 5th largest automaker (as of sales volume).
At a time when accelerating global management from 2005 to 2010, all eyes were on HMG. In April 2005, the cover story of Time Magazine featured the Group’s strategy of making inroads into the global market along with quality management. Forbes also said, "Hyundai Motor's ambitious move puts pressure on the global automobile industry, including the Detroit Big three carmakers". Motor Trend, an American automobile magazine, adopted Hyundai Motor as the one that the world should keep an eye on at the place of choosing the ‘Car of the Year’ in 2006.
Since the global market was changing rapidly, creative thinking and fearless spirit of challenge became a must to survive. HMG, which was committed to becoming a future winner and trailblazer, started to run an integrated steel mill in 2010. This was the world’s first ‘one-stop system’ capable of producing from molten iron to automobile. The true vertical integration ranging from materials, components to automobiles was finalized by rolling out high-quality automotive steel sheets at the Dangjin integrated steel mill in Hyundai Steel and laid the foundation for enhancing the competitiveness in the global market.
Furthermore, running the integrated steel mill added significance to HMG by completing the world's first resource recycling business structure. Each business field such as steel-components-automobile-construction established an organic resource circulation system: manufacture molten iron and steel plate (Hyundai Steel) → produce/scrap automobiles (Hyundai Kia) → produce steel products for construction using recycled iron scraps (Hyundai Steel) → civil engineering & construction (Hyundai E&C). The system served the purpose of renewing the Group’s image as an eco-friendly management leader all around the world.
Integrated Steel Mill
The integrated steel mill in Hyundai Steel is totally equipped with three processes: ironmaking, steelmaking, and rolling. Electric furnaces that use an iron scrap as raw materials produce iron products for industry and construction, and blast furnaces that use an iron ore as raw materials make the best steel sheets for automobiles along with shipbuilding and home appliances. The futuristic Dangjin still mill is equipped with eco-friendly and advanced IT facilities such as the world’s first sealed raw material storages and off-gas power plants. It has developed and produced high-performance and eco-friendly automotive materials such as high-tensile strength steel and hot stamping.
In 2010, HMG ranked 5th in the world by overtaking Ford for the first time in ten years after setting the goal of ‘Global Top 5’. When no one could guarantee success, a small clue of possibility turned into a torch for success by adding the spark of hope called efforts. Production, procurement, and the market became globalized amid the meticulous design of localization with the aim of attaining its success in the global market. The corporate culture that readily chose changes when finding the slightest chance proposed a new value in the new era.