
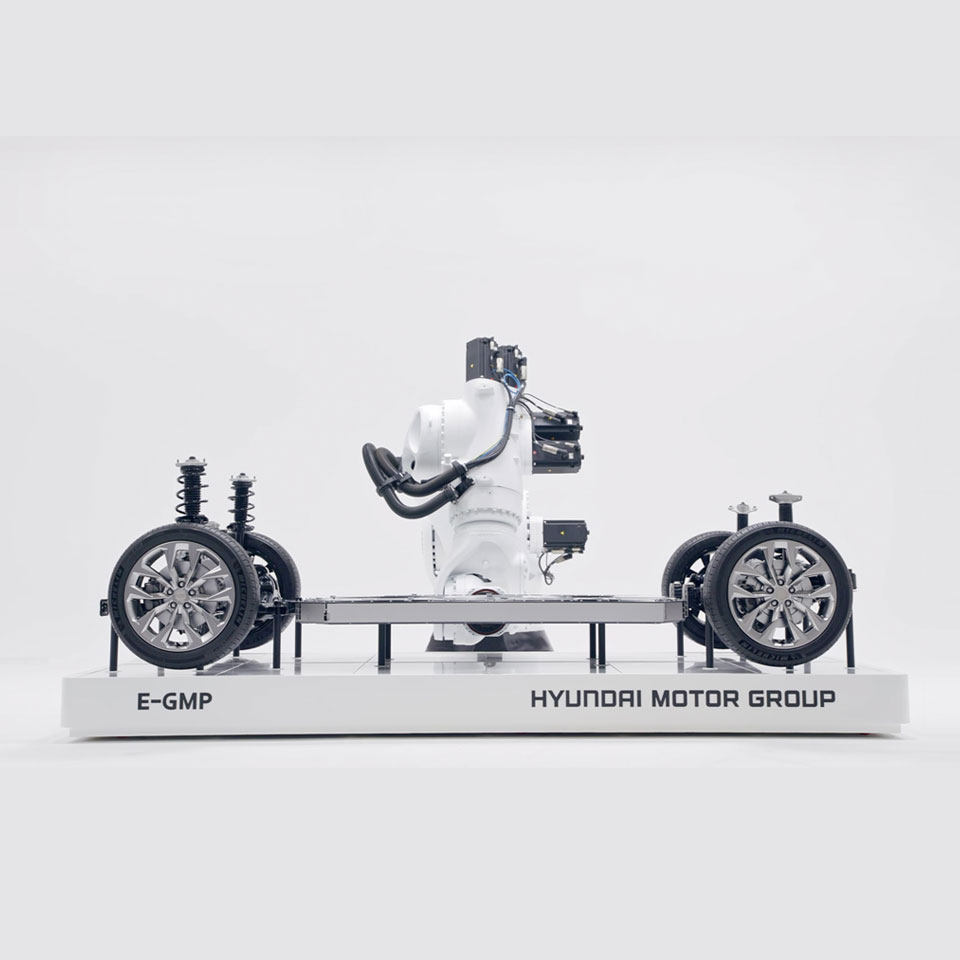
2022.01.17 EV
Nearly the whole world is setting rigorous regulations to come closer to the emission-free “Zero-Carbon Age,” and global manufacturers are diligently engaging in R&D to respond to this trend. EVs, which do not emit any exhaust, have emerged as the major environmental solution for the automotive industry.
Hyundai Motor Group declared 2021 as the year when its journey to global leadership in vehicle electrification begins. By 2025, the Group states, it will have released 23 eco-friendly vehicle lines and sold more than 1 million vehicles (or the market share of 10%). A concerted effort will be made to electrify the South Korean, U.S., Chinese, and European markets by 2030; developing markets like India and Brazil will have 2035 as the equivalent target.
These ambitious objectives are made plausible by the E-GMP (Electric-Global Modular Platform), Hyundai Motor Group’s first EV-exclusive platform. Platforms designed for EVs have serious ramifications on the EVs’ cost-efficiency and quality assurance, which explains why many global manufacturers have been focusing their R&D capacity to develop a single platform. The E-GMP is a culmination of all Hyundai Motor Group’s long-accumulated know-how in vehicle electrification. Compared to existing platforms—which were mere redesigns of ICEV platforms—the E-GMP is distinguished by many advantages: flexibility in development, EV-optimized structural design, standardized high-capacity battery system, longer range, futuristic aesthetics, and revolutionary cabin spaciousness.
Last August, Hyundai Motor Company unveiled IONIQ, the group’s EV-exclusive brand based on the E-GMP, and announced plans to sequentially release the IONIQ 5 (a compact CUV), the IONIQ 6 (a midsize sedan), and the IONIQ 7 (a large SUV). These new models are fulfillments of the value declaration made by the Group in the 2016 Geneva Motor Show, “Freedom in Mobility,” for which the group had launched a mobility innovation project by the same name, Project IONIQ. In that same year, the IONIQ model was released with the world’s first full eco-friendly lineup (HEV, PHEV, and EV); the IONIQ EV would later be crowned as the most energy efficient EV released in the U.S. in 2019. Following the philosophy and heritage of its predecessors, IONIQ was relaunched, in 2020, as a brand that would meet the needs of consumers seeking a modern, eco-friendly lifestyle.
The Kia Motors are also in the midst of executing the mid-long-term strategy ‘Plan S,’ shifting its direction to next-gen mobility and EV-based business models. The company has announced a plan to increase its proportion of EV sales to 20% by September of 2025, and it has also unveiled 7 model sketches of EVs that will see sequential releases through 2027.
When the driver turns on the car, the electricity in the high-voltage battery boots the vehicle and the systems power on in standby. When the gas pedal is pressed, the motor rotates and produces maximum torque. Then the EV transmission delivers the power to the wheels in accordance with the motor characteristics.
1. PE System
1-1. Motor
The equivalent of the engine in an ICEV, the motor produces the power by which the vehicle can run by converting the electrical energy in the battery into mechanical energy. The motor also serves as a generator during reduction, per the regenerative braking system*.
*regenerative braking system: converts the kinetic energy from elastic running (e.g. running downhill) into electrical energy, which is then stored in the battery. The system basically recoups, or regenerates, some of the energy spent during braking.
1-2. EV Transmission
The equivalent of the transmission in an ICEV, the EV transmission adjusts the number of revolutions by the motor, so that the electric vehicle can attain higher torque.
*EV Transmission Disconnector: the world’s first adaption on an EV vehicle, in which the motor and the drive axle can be connected or disconnected as needed. The mechanism enables free shifting between 2WD and 4WD.
1-3. Inverter
The inverter converts DC-power in the battery to the AC-power used for torque control in the motor. The inverter power module comes with Silicon Carbide (SiC) semiconductors* that are more efficient than the existing semiconductors made with Silicon (Si).
*SiC semiconductors: Power semiconductors that use cutting-edge material Silicon Carbide (as opposed to Silicon) to convert/process/control electricity. They are sturdier, higher in thermal conductivity, and better conserves energy than the previous-gen Si semiconductors.
2. Vehicle Charging Management System (VCMS)
A central component of V2L* along with the ICCU, The Vehicle Charging Management System oversees all vehicle functions related to charging.
*V2L (Vehicle to Load): A technology that enables the electrical energy from the battery to be used by external devices. The maximum power output is set at 3.5kW due to certain parts specifications. If an In-cable Control Box (ICCB) is used, the system can also slow-charge another vehicle’s battery (V2V; Vehicle-to-Vehicle).
3. Integrated Charging Control Unit (ICCU)
The ICCU is an upgrade over the OBC, which only allowed one-directional charging from an external source to the battery. It now allows bi-directional charging, enabling the aforementioned V2L function.
4. Vehicle Control Unit (VCU)
The VCU is responsible for controlling most vehicle functions dependent on electricity, including the control of the motor, regenerative braking, climate control, vehicle electronics, and power supply.
5. High-voltage Battery
The battery stores and supplies the electrical energy needed to power the car. Inserting more battery cells into the battery increases the vehicle range, but it also makes the vehicle heavier and more expensive. Finding the point of compromise that best fits the vehicle model is key. Recent advances in battery technology have seen the gradual rise of battery energy density.
6. 400/800V Multi-charging System
This patented system, applied to the E-GMP, is the first charging system in the world to allow seamless multi-charging between 400V and 800V. The default 800V Ultra High-Speed Charging requires 18 minutes up to 80 percent of capacity, yielding 500 km of range; just a 5-minute charge can yield 100 km. The system also supports the still-mainstream 400V High-Speed Charging, in which case it uses the motor and the inverter to convert the voltage from 400V to 800V before battery storage.
One source of inconvenience in driving an EV has long been the wintertime reduction of range: when the temperature falls, the resistance in the battery increases, leading to the reduction of range below normal levels. Moreover, unlike ICEVs, which can use the heat from the engine for cabin heating, EVs must use the electrical energy in the battery to do so, leading to a further loss of range.
Hyundai Motor Group sought to resolve these issues by developing a heat pump system with waste heat recycling, a step forward to the creation of a truly eco-friendly vehicle. The new heat pump system was installed in 2014 on the Soul EV for the first time, and it reduced the winter range loss by a remarkable 19% for the IONIQ EV. In addition, in part thanks to the heat pump system, the Kona EV came in first in the winter range test administered by the Norweign Automobile Federation (NAF).
To be fair, similar heat pump systems are used by most other global manufacturers. But there is significant variation in winter range loss per vehicle brand and model. Hyundai Motor Group’s heat pump system uses not only the heat from the external air but also the waste heat from electronic vehicle components—e.g. the motor, OBC, EPCU/PE Module, battery, and slow charger—to heat the cabin. In essence, this capacity for “recycling” puts the group’s heat pump system ahead of its competitors’.
EVs are often misunderstood by those, often unwarrantedly, concerned about electromagnetic radiation. Modern EVs are built with various safety measures to reduce the damage to their electronic components (and by extension, to passengers). Structurally protecting the battery from physical shocks, preventing component malfunctions from damaging the battery, and ensuring the safety of the charging port are examples of such measures.
Structural Protection of Battery Module
Most structural safety features work to protect the high-voltage battery from external physical shocks. The separator film inside the battery, which serves to separate the anode and the cathode materials and allows only the lithium-ion to pass via small pores, is thinly coated with ceramic for shock protection.
Pouch-type batteries were chosen to protect the battery from external heat, and the side seals on the either side of the battery were reinforced with shock-absorbing materials. For 800V ultra-fast charging, the thermal management technology of the battery system is important, and for this purpose, the split cooling channel structure has been applied to the system.
Four Rigorous Validation Tests of EV Battery
Battery’s Fail-safe Design
The EV battery interacts with the vehicle’s other electronic components to function, so one component malfunction has a way of “spreading” to the battery. The fail-safe feature exists to prevent such spread of damage from other parts to the battery. When abnormalities are sensed in the battery, the battery power is turned on or cut off automatically via a relay (electric switches that open and close circuits under certain conditions).
Safety Features of the Charging Port
Is it dangerous to charge an EV in rain? Not quite. Our EVs come with the 4-stage system for electric shock prevention. When the button on the charging gun is pressed, the electric flow is cut off immediately to prevent the damage to the connector area; unwanted liquid intakes like rain are discharged via the drain hole inside the charging port; the charging system only initiates charging after a set delay following the confirmation of proper connection to the charging port; and finally, upon inserting the charger to the port, the connector area is sealed watertight to prevent the seeping of unwanted liquid during charging.
The E-GMP is Hyundai Motor Group’s first EV-exclusive platform that, through modularization and standardization, can more quickly respond to the increasingly diverse needs of the market. The platform allows EVs to maximize the strength of the stable driving performance characteristic to their segment; it also ensures the safety of the passenger in a durable car body, not to mention providing the spaciousness unheard of in an internal combustion engine vehicle (ICEV). The faster and more efficient charging experience, as well as the battery’s ability also makes the platform a lifestyle-changer for consumers on-the-go.
These innovations were made possible largely thanks to the PE System, the compact-and-efficient modular battery/motor unit whose battery capacity can easily be altered to meet the particular needs of target car models. Hyundai Motor Group is currently collaborating with a number of capable battery makers to refine the platform, which, the group believes, will serve as the turning point that takes us beyond the EVs to the new age of smart, autonomous mobility.
E-GMP comes with the PE System, developed to maximize the driving performance of electric vehicles. The PE system, roughly the equivalent of the ICEV’s powertrain, comprises the motor, EV transmission, inverter, and battery.
The system can be described as having four major characteristics. First, it’s compact. With the motor, EV transmission, and inverter incorporated into one body, the system eliminates the waste of redundant space, thus reducing the vehicle weight. The number of parts that make the battery was also reduced compared to the existing batteries, and this compact battery module further helps E-GMP to optimize the EV’s ever-important range statistic.
Second, it’s efficient. The motor is now much more efficient, which allows the vehicle to travel farther with the same capacity battery. The coils inside the motor received the ‘Hairpin Winding’ technology, which made the power generation more efficient, and the cooling method was changed into a faster and more efficient oil cooling system whereby lubricant used in the EV transmission is cooled and sprayed directly onto the motor.
Moreover, the inverter power modules are now equipped with the highly efficient SiC(silicon carbide) power semiconductors to maximize the vehicle range, and the front wheels received the world’s first EV transmission disconnector system that allows the vehicle to shift freely between the 4WD and the 2WD driving modes.
Third, it is convenient. The E-GMP developers explored many ways to make vehicle charging as hassle-free as possible. The result of that exploration is the addition of the 800V Ultra High-Speed Charging system that, together with the mainstream 400V charging, makes up the E-GMP’s multi-charging system. Most existing charging stations use 400V charging, but 800V charging is making headways, particularly in parts of Europe. Hyundai Motor Group’s E-GMP is the world’s first multi-charging system that, by using the built-in motor and the inverter, is capable of accommodating either 800V or 400V charging without the need for extra equipment or manual adjustment. Its 800V Ultra High-Speed Charging requires 18 minutes up to 80 percent of capacity, and only 5 minutes to deliver 100 kilometers in driving distance.
Finally, it is fun to drive. The fun is obvious in the ‘High Response’ Motor system under 4WD. E-GMP comes with a high-output motor in the rear wheel and another motor in the front wheel, enabling 4WD. The motor was positioned lower than usual and this efficient weight distribution and the low center-of-gravity design allows the vehicles with E-GMP to turn sharp corners and run at high speeds more stably. In addition, the rear-wheel multi-link and the Integrated Drive Axle (IDA) complete the E-GMP by dramatically enhancing the R&H (Riding & Handling) performance.
The E-GMP divides the platform into separate zones, each of which is responsible for a certain safety task. First, the ‘energy absorption zone,’ stretching from the back beam to the subframe rear-mounting, was designed to invite the deformation of the body and the chassis to better mitigate the external shock. On the contrary, the ‘Lower-support section’, spanning the subframe rear-mounting and the dashboard, was designed to avoid the shock load to better protect the PE module and the high-voltage battery in the chassis area.
Finally, the ‘battery protection zone,’ spanning the dash and the high-voltage battery, comes with ultra-high-strength steel reinforcement to protect the battery. First, to protect the passengers, the cabin was designed in the A-pillar load distribution structure to resist deformation; the front subframe and the fender apron’s connection was reinforced in the same vein. To improve safety in small overlap crashes, a new crossbar structure was installed that connects the right and the left of the engine room, and the side-member cross-section was expanded to increase its stiffness.
The battery, too, obviously requires special protection as well during crashes. The front and the sides of the battery received increased applications of hot-stamped material, and extruded aluminum was applied inside the side seal to further protect the battery. The rear plate of the battery case was made of aluminum, and the center of the case was connected stoutly to the car body, allowing for a structure with a capacity for efficient shock absorption.
The E-GMP is stylish, with the short overhang and the longer wheel-base that contribute to a design befitting modern EVs. But its evolutions also meet the increasingly rigorous global safety standards, not to mention the spaciousness for realizing new automotive lifestyles.
The E-GMP’s capacity for design flexibility also can deliver new automotive lifestyle experiences for the passengers. The bulky internal combustion engine has been replaced by a compact motor, and the voluminous climate control system has moved into the engine room (or, to be exact now, the PE room) in split-type to occupy that space. The floor has flattened, with the battery placed lower and the center tunnel eliminated, and the resulting freed-up space was enough to ensure large leg-rooms for all seats, and particularly the rear seats.
This flat floor structure, though, could mean more than just legroom; because it essentially allows the rearrangement of the seats themselves, the designers are free to pursue unprecedented interior designs that match the vehicle’s purpose and the target consumers’ lifestyle needs; in other words, vehicle electrification may quickly be followed by the pioneering of new ways to experience life-on-the-go.
Imagine making your vehicle a “man cave,” complete with an assortment of smart digital devices; you might even turn your vehicle into a mobile office. Best illustrating such potential is the ‘45 Concept,’ Hyundai’s all-electric vehicle with a cozy modern interior space. Featuring wood, textile, and leather material, the cabin space is redolent of homely warmth—a place where one can take a breath and rest.
Year | History |
---|---|
1991 |
|
2010 |
|
2011 |
|
2014 |
|
2016 |
|
2018 |
|
2020 |
|
2021 |
|
2025 |
|