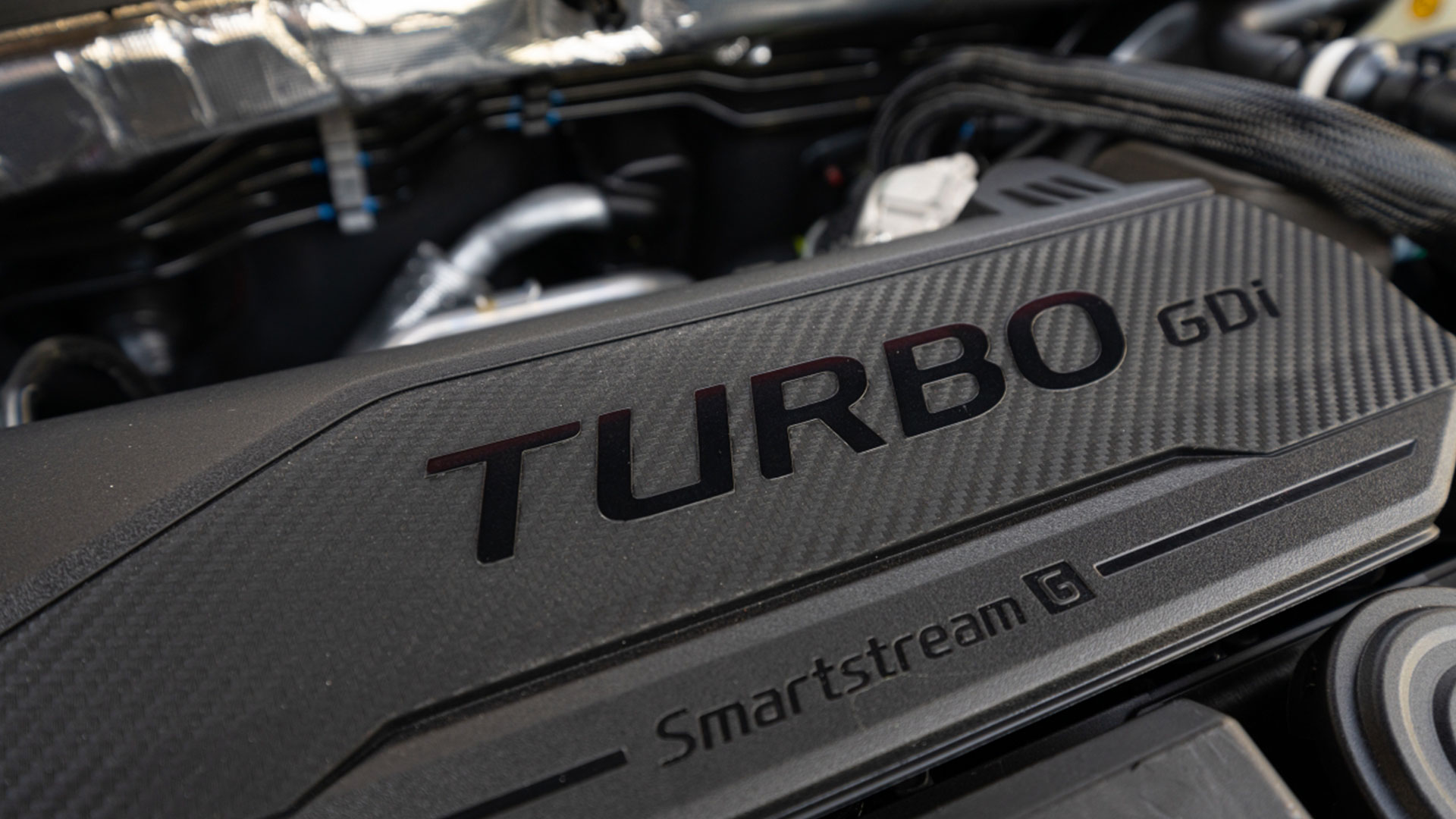
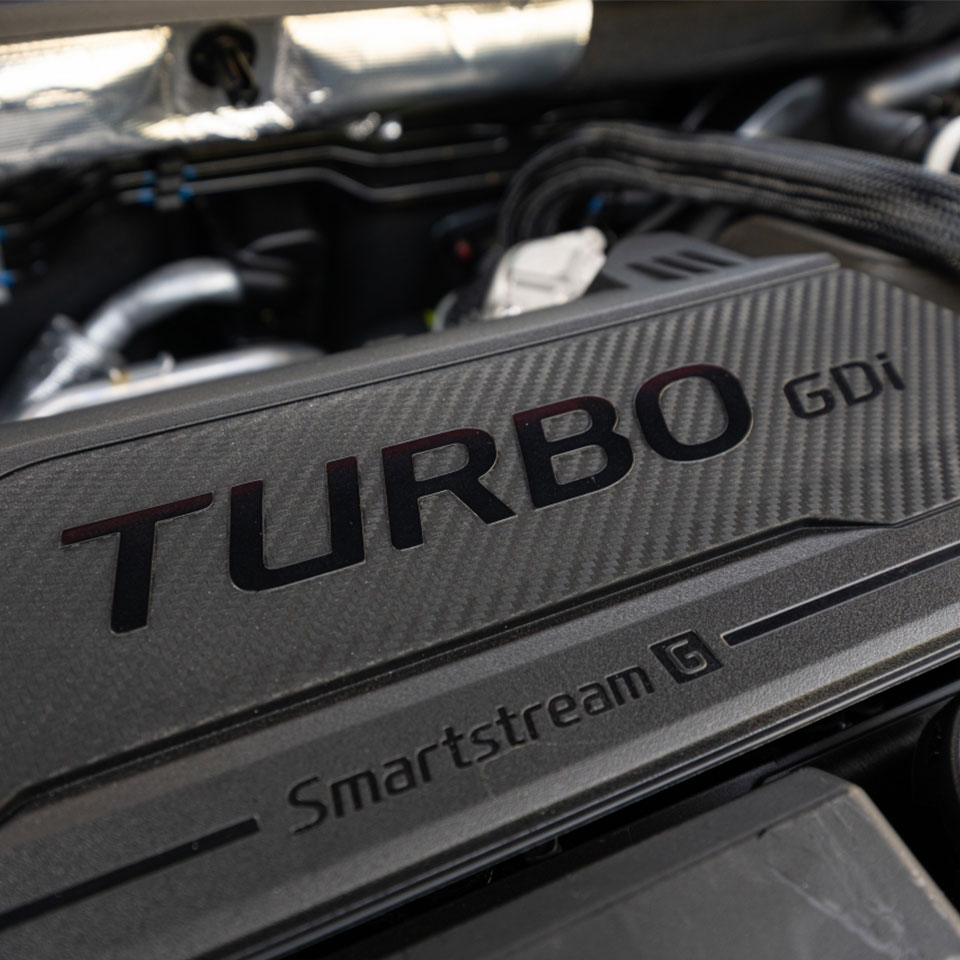
2020.09.03 Hyundai Motor Company
The engine is the heart of a vehicle. The role of engines is immensely important. Even if a car is well-designed, or has comfortable cabin and various convenience feature, it won’t be valuable if it is not powerful enough due to the poorly made engine. In addition, even though the chassis is high quality, it will not be fun to drive the vehicle if the engine is not good enough. In the era of eco-friendliness, the role of engines hasn’t been more important. This is because an engine should be efficient while maintaining performance to increase fuel efficiency and reduce emissions. However, making such an engine is not as easy task.
To the extent, Hyundai’s latest engine is noticeably improving. The evidence is that objective figures such as maximum power, maximum torque, fuel efficiency, and carbon dioxide emissions have improved. It is also proving its excellence by making it the annual Engine of the Year award selected by media such as 'Wards Auto.'
Among the many reasons why Hyundai’s engine quality improved recently, the most notable factor is the participation of the WRC. As introduced in the past three WRC technology internalization contents, Hyundai has accumulated a variety of technologies and know-hows in building its own race cars since returning to the WRC in 2014, and has applied them to mass-produced vehicles. The story is the same when it comes to the engine technology. The engine technology of the WRC Rally car, which drives at speed, is applied in the mass produced vehicles and constantly improving its performance and efficiency.
Currently, Hyundai's WRC Rally car is being developed by Hyundai Motorsport GmbH located in Germany, but many of the tasks regarding engine development, including durability improvement, performance testing, and analysis of the race car engines, are being conducted in collaboration with Hyundai Motor Group's Namyang R&D Center in Hwaseong, Gyeonggi Province.
In the early 2010s, when Hyundai Motor was preparing to return to the WRC, Namyang R&D Center took charge of most of the development work of race cars. Therefore, researchers who were making engines for mass-produced cars often participated directly or indirectly in developing engines for World Rally Cars, and researchers began to ponder how to apply this experience and technology to the development of engines for mass-produced cars.
The same goes for Kim Jong-hyuck and Han Yung-hee, Senior researchers at Advanced Engine Development Team. They also participated in the development of the Gamma engine on the initial World rally cars, and also the engine that are currently on the World rally cars. At the same time, they are in charge of leading the development of the engine for mass-produced vehicles. They developing various engines for race cars and mass-produced cars altogether. I met two researchers who are leading the way in internalizing mass produced vehicles of WRC technology and talked about internalizing engine technology.
Q. What is the biggest difference between the engine of the World rally cars and that of the mass produced cars?
Senior researcher Kim Jong-hyuck(hereinafter referred to as Kim Jong-hyuk) | The biggest difference is manufacturing methods and materials. We mass-produce the engines for the mass-produced cars. But we can’t do that for the race car engines because we need to customize engines with expensive materials for only a few race cars. On the other hand, the engines of the mass produced cars cannot use expensive materials to meet prices.
The World rally car engines also use new technologies that have not been used for mass produced cars, which is solely for better results. It becomes an opportunity to test the new technology applied to the engine and accumulate data through various feedbacks through the WRC rallys where cars drive under harsh conditions. This data, in the end, can be used in mass produced cars over time, which is internalization.
Q. One of the difficulties in internalizing the technology came from races into mass-produced cars would be that we can’t easily use expensive materials. What are the examples of internalization that have solved the cost issues?
Senior researcher Han Yung-hee(hereinafter referred to as Han Yung-hee) | There was a problem regarding the cost-efficiency when developing next-generation high-performance engines. After developing turbochargers with technology inspired by car races, the unit price was too high to be applied to regular mass-produced vehicles. Therefore, we came up with a method that reduces the unit price of parts by securing more supplies.
Some technologies are still finding cost-effective solutions. It's about camshafts for high-performance engines. The camshaft is literally the shaft which connects the cam of each cylinder that opens and closes the intake and exhaust valves of the engine, and the how the engine works depends on the shape of the cam. The valve is limited depending on the shape of the cam, and we confirmed that the engine power is improved by applying the cam which is used for the World rally cars to the high-performance cars. On the other hand, the expected durability of the engine applied to the World rally car, and that of the mass-produced car is different, and this was another thing to think about. To this end, we are internalizing the technology by applying some of the materials used for the WRC engine valve system.
It might seem like the shape of the cam has nothing to do with durability, but the speed at which the valve operates and the amount of impact varies depending on the shape of the cam, so it must be accompanied by a rigid material as well as a tricky fabrication technique. In the process, the cost issue is inevitable. Although it is difficult to change the shape of the cam just like we do with a race car, it also has the advantage of improving performance by simply applying it to the engine of the mass-produced cars. Therefore, the automaker is currently in the process of optimizing various factors to internalize the technology into mass-produced vehicles.
Q. The WRC often runs in harsh conditions, which leads to engine loads. Isn't there any internalization technology that you've gained from solving problems?
Kim Jong-hyuk | WRC Rally cars are not free from cooling problems because they run a lot in hot weather areas and use high-performance engines. One easy way to solve this problem is to increase the amount of air flowing into the front of the vehicle. Therefore, the air intake of the bumper is raised at a line that does not interfere with airpower performance to solve the cooling problem. However, this method cannot be applied to mass-produced vehicles. This is because bumper designs must meet the crash safety standards in many countries around the world. So, instead, we are trying to improve the shape of the block water jacket and optimize head cooling to improve the cooling efficiency of high-performance mass-produced engines.
For high-performance vehicles, the consensus of all employees on design and vehicle performance is of paramount importance in order to secure an additional opening area at the front of the vehicle. To this end, the company is actively collaborating with not only the design but also with the to vehicle development.
Also, it is not easy to solve the oil lubrication problem in World rally cars. Due to the nature of the WRC, which is frequently issued because of its heavy weight-centered movement, such as strong lateral acceleration, race cars require separate oil circulation techniques. Some of the technologies accumulated while solving these problems were applied to high-performance N models so that oil circulation could be smoothened even in harsh driving conditions.
Q. The WRC Rally car engine is a four-cylinder. On the other hand, Hyundai’s mass-produced engine has a multi-cylinder engine in addition to the four. Isn't there a case of internalizing race car technology in developing these multi-cylinder engines?
Han Young-hee | There was a talk about building another high-performance engine based on the technology and confidence built up by creating a high-performance World Rally Car engines. In that way, the company completed the advanced development of the eight-cylinder engine, which is as powerful as a supercar. The engine is equipped with the crankshaft and valve seat technology used in the WRC Rally car engine. Internally, however, it has already confirmed that it can make a world-class eight-cylinder engine, but it is putting the application on hold for a while because the development of applicable models has not yet been carried out.
One might wonder why the company uses a lot of time, money, and human resource to develop high-performance multi-cylinder engines in advance, even though there are no models that can be applied immediately. The reason is simple. This is because the timing is late if the engine is developed after the new car project begins. So we made a high-performance engine preemptively with various possibilities in mind. Of course, this was possible thanks to the high-performance engine development skills and experience accumulated through the WRC Rally car.
Q. Is there any engine developed through this similar process?
Kim Jong-hyuk | Of course there is. It is a high-performance engine currently under development, and started development even before the N brand was launched. This is through the Racing Midship (RM), a project that Hyundai Motor has undertaken to develop technologies related to high-performance cars. The timing of the start of the project RM coincides with the time of re-entry into the WRC. In other words, the technology accumulated while building the engine of the WRC Rally car has been verified through the project RM, thus completing much of the high-performance engine technology in advance. Meanwhile, some of the technologies built up through this process have been applied to the 2.5-liter turbo engine that is currently being mass-produced. As a result, it helped to enhance the performance and durability of some parts.
Q. As we have talked so far, the process of developing race cars and mass-production cars is different. However, he must have felt and realized a lot in the process.
Kim Jong-hyuk | In the early days of the engine development of the WRC Rally car, he collaborated with Hyundai Motorsport GmbH located in Germany. Thanks to this, I was able to get a lot of help in developing a rally car engine. The view has widened and the way of thinking has changed. Above all, I have gained confidence. There was a huge difference in that they learned new technologies and know-how that they had never experienced at the site of the development of mass-production vehicles.
There were other factors as well. It was a huge competitive drive at the WRC site. Everyone struggled to make the overall part of the body, including the engine and chassis, a little lighter, faster and stronger to beat other teams and manufacturers. To do so, I realized that I needed a way to get ahead through new attempts and challenges, not through imitation.
Han Young-hee | A typical example is a change in the injector position of the race car GDI engine at the beginning of WRC participation. All of Hyundai's GDI engines had injectors located on the intake valves. However, due to interference with the intake valve, this method had many points to pay attention to under injection conditions such as injection timing. In order to improve the efficiency of the intake air and optimize the fuel injection pattern while breaking away from these constraints, Hyundai has moved the position of the GDI engine injector of the WRC Rally car toward the exhaust valve for the first time. Despite many twists and turns in the course of this new attempt, the result gradually boosted the performance of the race car, which eventually led to the excellent performance of the i20 WRC Rally car.
It was all a new experience for us back then. By directly participating in the development of the race car, we have developed our own will and passion to make better cars than other manufacturers. This mindset continued even after returning to Namyang Research Institute. I wanted to make cars that were better than other manufacturers, as I did when I developed the WRC Rally car. I think that the mindset to beat other teams was naturally internalized and that when developing mass-production cars after returning to Namyang R&D Center, they were able to demonstrate different capabilities from the past.
Examples of high-performance mass-production vehicles with embedded WRC technology
Let me introduce more specific examples of the internalization of WRC technology mentioned in interviews with Senior researchers Kim Jong-hyuck and Han Yung-hee.
Cooling and oil circulation technologies that maintain engine performance even under limitations
The WRC Rally car has a lot of heat load on the engine. To solve this problem, several heat management technologies and methods have been developed, some of which have been applied to 2.0l turbo engines of high-performance N models. Thanks to this, i30 N or Veloster N rarely experience performance degradation even after a long circuit.
The typical technology internalization part is performance improvement through the intake and exhaust optimization. It was difficult to optimize this in terms of package or cost when developing current mass-production vehicles. However, while gaining experience in developing high-performance cars, many efforts have been made to find areas that are lacking in order to improve performance from a company-wide perspective. In particular, engine responsiveness could be improved quickly by optimizing the intake airflow path that supplies air to the engine and improving the intake sensor.
In addition, the cooling performance was improved by optimizing intercooler efficiency, and the pressure of the catalyst and exhaust system was reduced by lowering the compression ratio compared to previous ones in order to fundamentally prevent performance degradation in hot air intake situations. At the same time, the ECU program has been refined to optimize engine movement according to intake air temperature. The vehicle development department also made efforts to improve the overall exhaust system's internal diameter without missing any details such as forming the weld bead outward in cooperation with the officials.
One of the important things about high-performance engines is engine oil circulation. High-performance mass-produced cars need to strengthen the engine oil circulation system compared to regular cars due to their fast acceleration, reduction, and frequent cornering. This is because the oil in the pan is pulled to one side by centrifugal force. The dry sump oiling system of the WRC Rally car engine is a good alternative, but the high price makes it difficult to apply as it is. Thus, in the case of high-performance mass-production vehicles, the shape of the oil pump inlet and oil pan were optimized by adding test conditions to ensure oil supply stability in circuit conditions from the development stage. In the process, the oil circulation technology of the World Rally Car became a great reference, and as a result, we were able to maximize durability without significantly increasing costs.
High-performance cars often reaches the maximum torque compared to ordinary cars. However, it is not easy to randomly increase the engine's rev limiters. This is because the more it rotates, the greater the kinetic energy is created. Therefore, increasing the number of torque by just 500 rpm will increase the load in the engine due to the increased kinetic energy. In general, the turning limit of the World Rally Car engine reaches 8,500 rpm. In developing the engine, Hyundai has built up know-how on technology that increases the number of rotations and lowers the load. For example, it has secured a technology that increases the stiffness of moving parts such as crankshaft and valve and reduces resistance. Embedded in high-performance turbo engines, the technology is being developed to allow the pre-developed 2.3-liter turbo engine to spin up to about 7,000 rpm, a very high level by mass production vehicle standards.
Since Hyundai Motor returned to the WRC in 2014, as seen in a total of four WRC technology internalization contents, there have been considerable changes in Hyundai's mass production vehicles. It is a sharp improvement in performance in two areas, engine and chassis. Above all, Hyundai Motor's WRC challenge is meaningful enough, given that researchers who develop cars have improved their skills and that the way of thinking in the process of developing vehicles has changed significantly.
For your information, this year's WRC will be scaled down to seven rounds in the aftermath of Corona 19. The start is the fourth round of the Estonia Rally, which runs from Sept. 4-6. The Estonia rally, which was scheduled to be added to the WRC calendar for the 2022 season, was pulled due to scheduling due to Corona 19. The Estonia rally is expected to have many variables and upsets because of the resumption of the WRC in about seven months and the fact that it is the first place for the WRC.
However, the variables and anomalies of the Hyundai team are expected to be relatively small. The first reason is that Ott Tanak, who joined the Hyundai team as a driver since this season, is from Estonia. Of course, the fact that Ott Tanak was the defending champion of last season cannot be ignored, either. Above all, the biggest advantage is that Hyundai's rally cars perform very well. Let's hope the Hyundai team will give good news at the Estonia rally, and let's also watch their performance in the WRC for the rest of the season.
All-rounder, high-performance SUV: Hyundai Kona N
2021.06.25 16min read