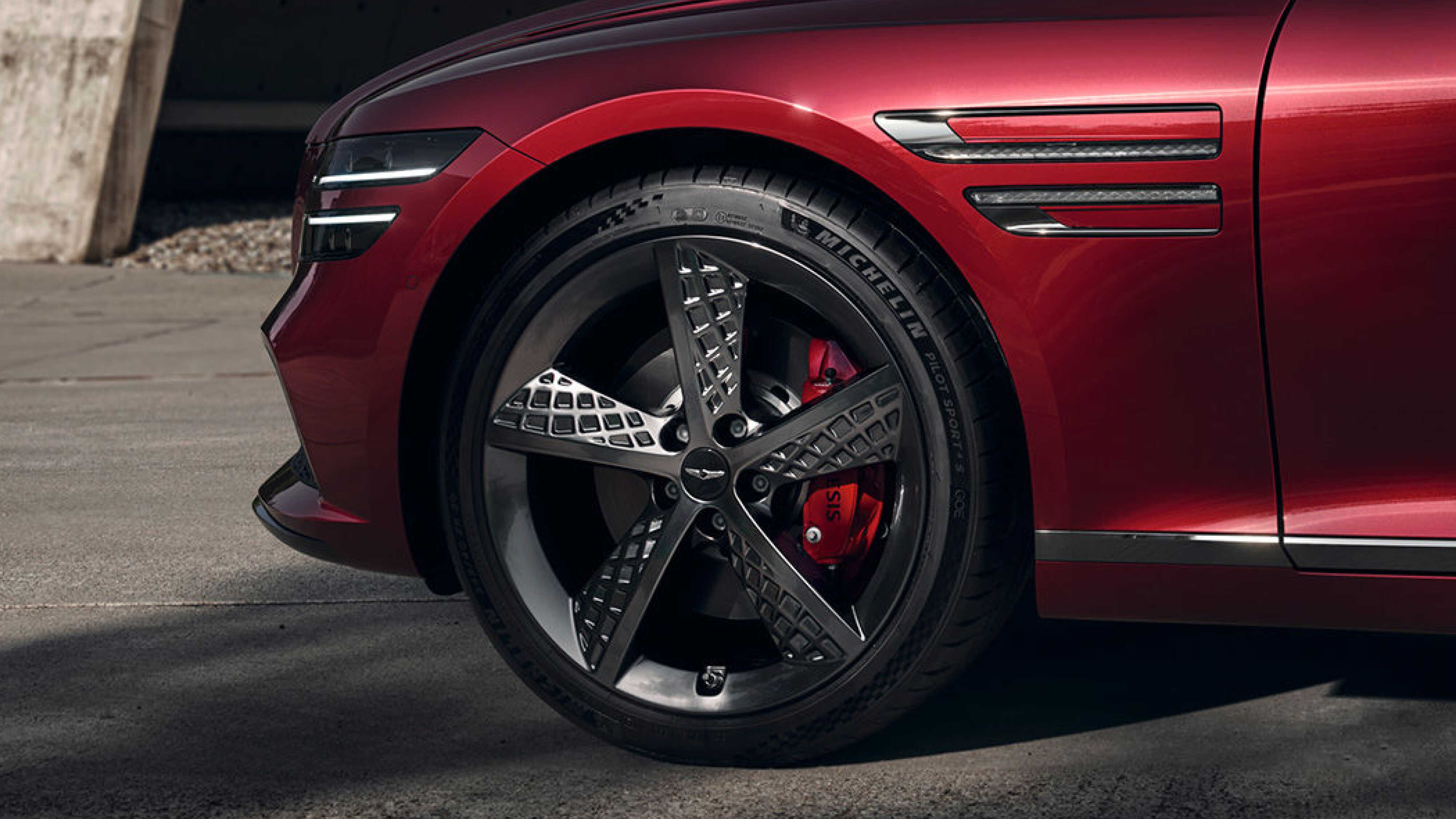
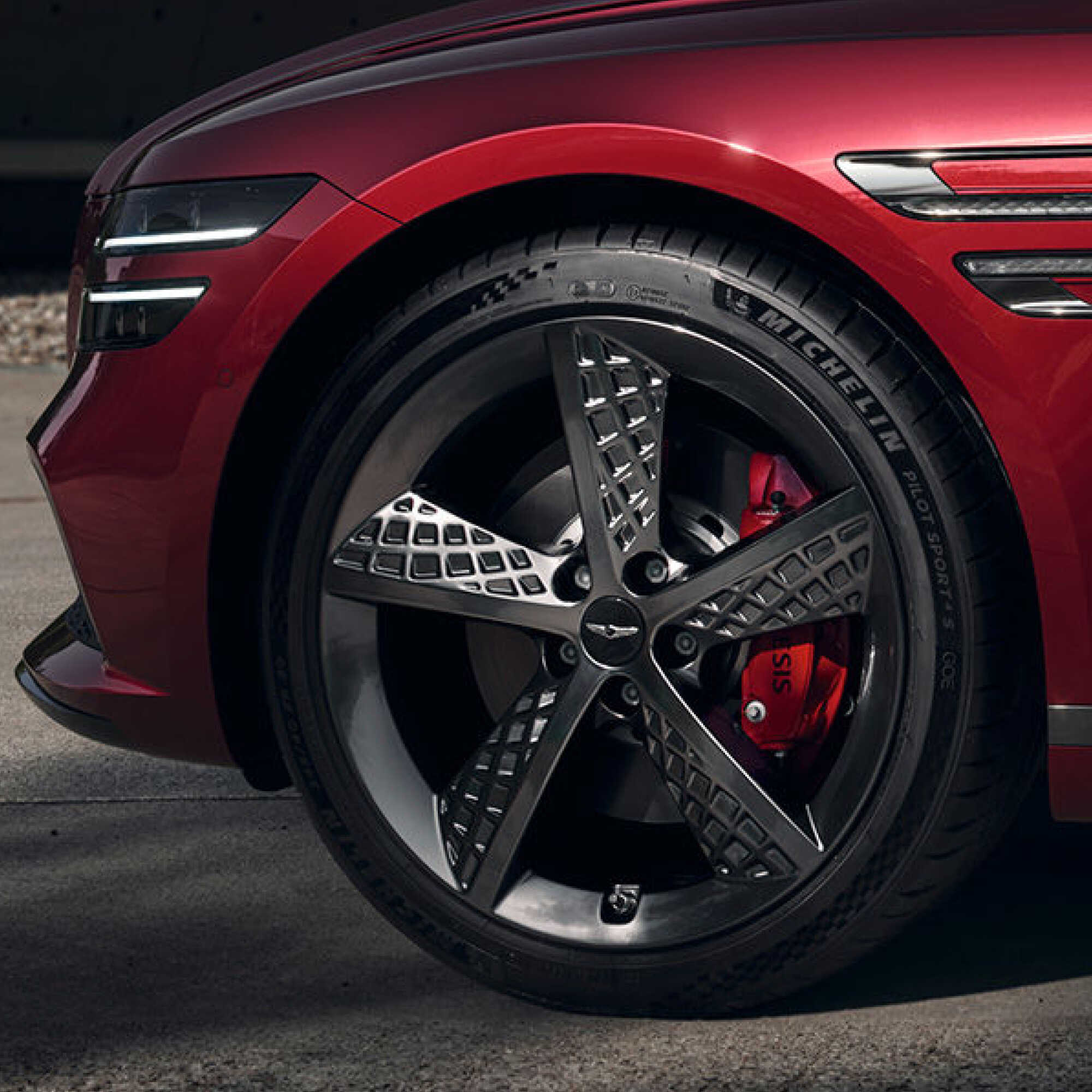
2023.03.21 Hyundai Motor Group
The most important abilities of a car are to drive well and stop well. The essence of a car is about mobility and safety, so these things must be perfect. However, there is no need to upgrade the brake system of a car to a high-performance system; like many other parts of a car, brakes must strike a balance between performance and practicality. For example, if the brake system were to increase in size, the wheels and tires would have to increase in size as well because this would affect not only driving characteristics but also maintenance costs such as fuel economy. For these reasons, cars need appropriate brake system.
The brake system uses friction to reduce speed. Therefore, the components used in the brake system are broadly divided into, ‘parts that are in contact with friction for braking’ and ‘parts that provide the force necessary for friction.’
The parts that come into contact with friction are classified according to their structure and affect the characteristics of the brake system. There are two main methods used for cars: the caliper method, which is commonly referred to as the disc method, where the brake pad (a pad-shaped friction material) is brought into contact with the exposed disc (a disc-shaped brake friction material) to reduce speed, and the drum method, which is not exposed externally. In this method, a brake lining (a semicircular-shaped friction material) is attached to the inside of a disk-shaped case that has friction material on the inside, and the brake lining is pushed outwards to come into contact with the friction material when needed to reduce speed. Both methods have their advantages and disadvantages, but the caliper method is mainly used for passenger cars because it is exposed externally, which allows for good heat dissipation, and shows consistent braking power even when used repeatedly.
The parts that supply the force (braking power) to the parts that come into direct contact with friction, such as the caliper, brake pad, and disc, are also classified into two types according to their operating methods: the master cylinder and booster (MBSTR) and the integrated electric booster (IEB).
The master cylinder and booster mainly maintain the booster’s interior in a vacuum state using the intake pressure of the engine. When the driver steps on the brake pedal, external air is introduced into the vacuum state inside the booster, which forcefully pushes the plate inside. This utilizes the pressure difference to deliver a force stronger than the force applied by the driver on the brake pedal. The force pushed out in this way is transmitted to the brake caliper through the fluid (brake fluid).
On the other hand, IEB gives power using an electric motor. Although it transmits braking force using fluid like the master cylinder and booster, it does not require an engine. Some of the internal combustion engine cars, hybrid cars, electric cars, and hydrogen fuel cell cars of the Hyundai Motor Group use IEB.
As mentioned earlier, the brake system differs slightly depending on the car. It is optimized according to the weight and drive specifications of the car. When planning a new car, after determining the major specifications of the car, targets for braking performance and heat capacity are set and development begins based on them. Therefore, it is not an exaggeration to say that each car’s brake is a customized specification. Kim Young-gwang, a responsible researcher at Hyundai-Kia’s Namyang research center’s braking design team, explains this as follows:
“Assuming that our customers drive to their limits in various driving environments, the car’s braking performance is determined; the car should be able to maintain a short stopping distance even on wet or snowy roads. Also, it should ensure that the braking force does not decrease even if the car repeatedly brakes in maximum load conditions or when continuously pressing the brake pedal on a long downhill road. Medium-sized cars generally have a conventional caliper system. However, when the vehicle weight or engine output increases, the braking system’s performance should also be enhanced. Therefore, models of the Genesis brand, such as Hyundai Motor’s N models or high-weight/high-performance cars, even among medium-sized cars, have a large caliper specification, and some trims even have a popular mono-block caliper.”
However, a larger brake is not always better. When brakes get bigger, the wheels and tires are affected as well; if the weight of the vehicle becomes heavier, it can affect the performance and fuel efficiency. Therefore, high-performance/large vehicles need to ensure sufficient cooling performance to optimize the size of the brakes. Therefore, technologies such as cooling ducts that cool brakes with air are important.
In addition, the design of the brake system of an electric car has two goals different from that of an internal combustion engine vehicle - the first is improving fuel economy. In order to go as far as possible with limited energy, the resistance must be reduced. However, in a typical brake system, some resistance is created while the brake pads return to their original position after the caliper is operated. Thus, an electric vehicle’s braking system improves its efficiency by increasing its speed. And this is made possible thanks to the integrated electric booster. Since the driver’s sensations during braking are implemented in the simulator, there is no discomfort in pedaling even when the return speed increases.
The second is the thermal capacity of the disk. Electric vehicles use the braking torque of the motor together during braking - regenerative braking - so the heat load is smaller than that of internal combustion locomotives. However, since regenerative braking does not intervene when the battery is fully charged or in N gear, the brake system must be designed with this in mind. The regenerative braking system also reduces the wear rate of brake discs and pads. Therefore, studies on optimizing brake size are being conducted to reduce the thickness of discs and pads.
The brake system is not all about braking performance; When the brake pedal is depressed, both the emotional aspect and the driving performance must be considered, such as the braking sensation felt by the driver. The braking sensation is realized by coordinating the master cylinder & booster and the integrated electric booster. However, parts may differ depending on the characteristics of the model.
Regarding this, Senior Researcher Kim Gwi-cheol of the Brake Testing Team at the Namyang R&D Center of Hyundai Motor Company and Kia Motors added the following explanation, saying, “The goals and orientations of the brake system are different for each model, and must be adjusted accordingly.” “In the case of an electric vehicle, the braking sensation can be changed depending on the mode. For example, Sport mode makes the braking feel sporty as well. Depending on the tuning, both normal braking and sporty braking are possible.”
In the case of the Kia EV6 and EV6 GT, the performance of the brake system was determined according to the power performance. For example, the EV6 GT uses regenerative braking up to the high deceleration range, which is to increase fuel efficiency in harsh conditions such as circuit driving. On the other hand, electric cars in the past and now have a different feeling when you step on the brakes. By continuously improving the hardware and software of the integrated electric booster, the braking sensation has become more natural.
Reducing the weight of the brake system also contributes to changing ride comfort - like the brake discs made of hybrid (cast iron/aluminum) material developed by Hyundai Motor Company. Hybrid discs are lighter than current products and help improve riding comfort.
“The development goal of the hybrid disc was lightweight design. The friction surface of the disc originally used cast iron material, but the part that attaches to the wheel bearing was made of aluminum material to reduce weight. Currently, Genesis models have hybrid discs. The weight of the structures located below the suspension springs (unsprung mass) is a significant factor affecting ride comfort, so the hybrid disc improves driving feel,” explains senior researcher Kim Young-Kwang.
*Unsprung mass: the lighter it is, the better the ride comfort and handling
The most important part of the brake is reliability, because it is a part that is directly related to the safety of the vehicle. In addition, it is necessary to secure performance and durability so that it can respond to various environments around the world. In addition to extreme climates such as severe cold or heat, it must show its original performance without change even when running on rough roads such as sand or mud.
In addition, modern brake systems also focus on control design. It is linked to various functions such as vehicle attitude control functions such as ABS and ESC, autonomous driving, parking assistance, and electronic parking brake (EPB). Therefore, it is necessary to accurately satisfy the requirements of each function.
For this reason, brake development and new car development projects have a lot in common. Once the weight, driving system, and braking target of the new vehicle are determined, various parts are designed to fit the structure of the vehicle, and a controller is developed to perform cooperative control. Afterwards, performance tests and quality checks are conducted according to the development stage. In this process, different departments work together to find problems and then solve them; A good car isn’t just finished one day.
Researcher Kim Young-gwang says that the most difficult part of brake development is “quality”. In the brake development stage, there are often problems that arise for unknown reasons, and it takes a lot of effort to solve them. “Recently, we were worried about putting brake fluid in the brake hydraulic line. If air enters the brake hydraulic line, it can have a negative effect on braking sensation. However, the electronic control hydraulic unit (HECU) has narrow and complicated internal circuits, making it difficult to remove air. Therefore, we had to try several operating patterns during the injection process. Recently, we utilized a new brake fluid injection pattern for quality improvement, and I learned a lot in this process,” says researcher Kim.
Kim Gwi-cheol, a senior researcher, also expresses a similar sentiment; “When the ideas that I have thought hard about are reflected in actual car design, I feel a lot of satisfaction. Moreover, when these ideas work well with various systems, I am grateful to all my colleagues. Many control strategies related to regenerative braking have been incorporated in dedicated EVs released after the Hyundai IONIQ 5. When I see a car that contains everyone’s ideas and passion, I feel great joy.”
The latest brake trend is related to electric vehicles such as regenerative braking - like dual motor regenerative braking coordinated control technology in electric vehicles. It adjusts the ratio of hydraulic braking and regenerative braking within the set braking force, and distributes the braking force of the front and rear wheels of the regenerative braking. This maximizes efficiency while also increasing vehicle stability when braking. There are more advantages; When the hydraulic brake system fails, regenerative braking also supplements the braking force.
Autonomous vehicles need to be able to stop properly even if they break down. Therefore, the automaker is also developing technology that will allow the car to stop properly even if the autonomous driving controller or braking system fails. In addition, the Namyang R&D Center of Hyundai Motor Company and Kia Motors is conducting advanced research on cooperative regenerative braking control technology for self-driving vehicles with four motors. This can control not only the front-to-back distribution ratio but also the left-right distribution ratio during braking. Like the dual-motor regenerative braking coordination technology, this will be of great help in improving fuel efficiency and ensuring vehicle stability when braking. In the more distant future, eco-friendly electric brakes, which do not use brake fluid and independently control the braking force of each wheel, will also be available.
Hyundai Motor Group has been strengthening brake performance so that the car can accelerate as much as the driver wants and stop accurately at any time and in any situation. In addition, major foreign media outlets that value driving performance paid attention to Hyundai Motor Group’s excellent brake performance. Hyundai Motor Company’s IONIQ 5 surprised everyone by recording 34m when measuring cold and hot braking distance in its EV comparison test in the famous German automobile magazine 〈Auto Zeitung〉.
Not only did the IONIQ 5 break the 35m stopping distance, but compared to its rivals - both the BMW iX3 and the Audi Q4 e-tron - the gap in cold/hot measurements was huge, further highlighting its superiority. The Kia EV6 also outperformed its rivals in an electric SUV comparative evaluation conducted by 〈Carwow〉 and 〈Auto Motor und Sport〉, two well-known European automotive media outlets; The judges mentioned ‘strong braking performance’ as one of the secrets. Hyundai Motor Group will continue to strive to improve the basic performance of automobiles – running, turning and stopping – even in the face of strong waves of electrification and autonomous driving. Even if the automotive industry undergoes various changes, the essence of driving will remain the same.
Auto Zeitung Chooses IONIQ 5 and EV6 In the Comparison Test
2022.03.07 9min read