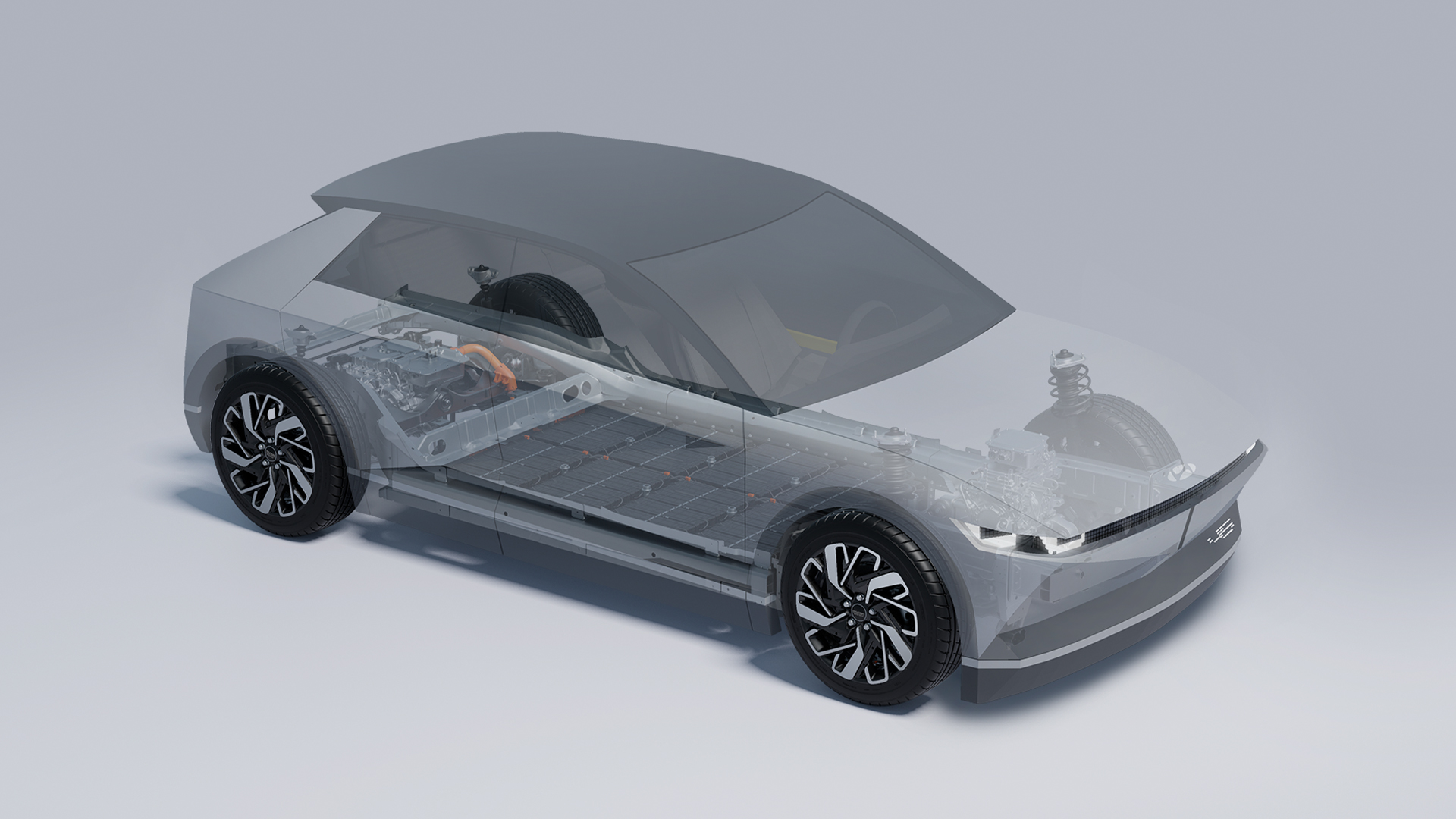
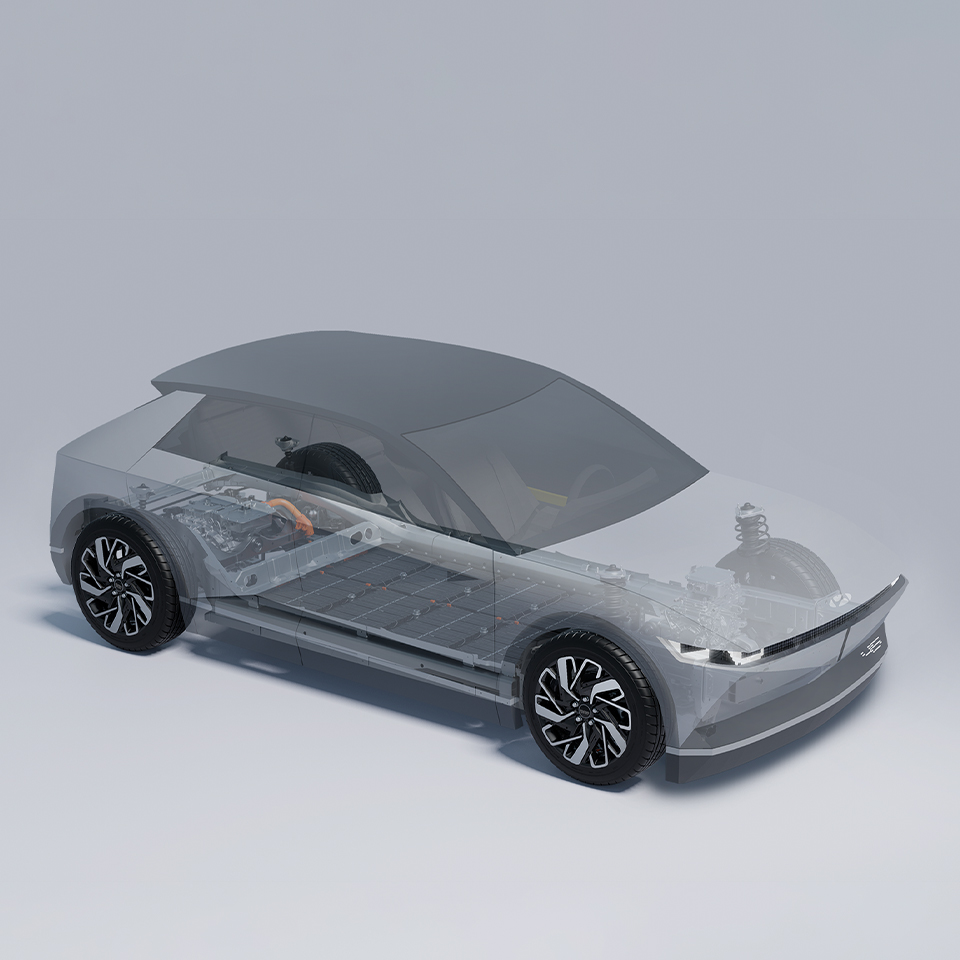
2020.12.02 Hyundai Motor Group
Hyundai Motor Group’s Electric-Global Modular Platform (E-GMP) is the foundation for the next generation of the group’s BEVline-ups and a symbol of the industry’s inevitable transition to eco-friendly vehicles. The implication here is that BEVs based on the E-GMP will outperform existing BEVs in unprecedented ways. Indeed, the very way in which the E-GMP is designed reveals stark differences to the BEV platform which is derived from internal combustion engine vehicle (ICEV) For example, the E-GMP has replaced the engine and the driveshaft – needed only in ICEVs – with space for the battery and motor. This BEV-tailored design gives several unique advantages to the platform; this article details five of these advantages.
BEVs based on the E-GMP boast a maximum driving range of over 500km.
The E-GMP can flexibly accommodate a variety of battery capacities to suit a vehicle’s segment and model characteristics. The maximum driving range for the highest-capacity layout is set over 500km. This flexibility is the result of E-GMP’s PE system*, with standardized battery modules that can be assembled in a variety of ways to create a battery pack that best matches the range expected for each model.
*PE (Power Electric) system, roughly equivalent to ICEV powertrains, comprises the motor (for power generation), EV transmission (reducer), inverter (energy conversion), and battery (energy storage).
Ordinarily, BEV batteries are composed along the following hierarchy. Battery cells, the most fundamental building block that stores energy, combine to form battery modules, which then combine to form battery packs that make up the battery. But the E-GMP standardizes the battery cell and module into one unit. Thanks to this standardization, damaged batteries no longer need to be replaced as a whole; only one individual malfunctioning module needs to be repaired or replaced selectively, reducing the cost of repairs. From a production standpoint, this has positive implications for quality control as well.
Moreover, the E-GMP boasts a 10% improvement in energy density compared to existing BEVs with the equivalent battery system size. The battery system is lighter and more compact, allowing more efficient use of space in vehicle designs. Altogether, these improvements hint at the platform’s innate versatility, accommodating any number of segments, models, and consumer lifestyles by adjusting the battery composition as needed.
Finally, the E-GMP’s outstanding range is partially a result of the world-class energy efficiency of the group’s cutting-edge PE system. One particularly notable feature of this system is the ‘hairpin winding technology’ applied to the coils inside the motor. A typical BEV motor is composed of a rotor (with a permanent magnet) and a stator (with the coil winding); power is generated by the rotational torque made in the interaction between the electromagnetic force from the stator and the permanent magnet on the rotor. An important observation: the tighter the coils are wound around the stator, the more efficient the power generation.
Hairpin winding technology takes advantage of this and making the coils tighter by utilizing hairpin-shaped coils with rectangular cross-sections. Compared to round coils with circular cross-sections, these coils can better “stack” on top of one another and reduce the empty space around the stator. In turn, this reduces the resistance around the winding, leading to a 10% improvement in the coil space factor (the ratio of available space occupied by the coil).
The E-GMP features technology which directly sprays cooling/lubricating oil, like a mist, onto the coil inside the motor to more effectively dissipate the heat.
In addition, the new PE system utilizes a new oil-cooling feature to boost efficiency. As in an internal combustion engine, an electric motor produces heat energy during power generation and needs an effective cooling mechanism. Overheating can deform parts and damage the motor’s functionality. Most motors have long utilized water cooling to indirectly manage heat. But coolant only flows within the motor’s housing in this instance, and therefore is unable to directly cool the hottest part of the motor – the coil. In contrast, the E-GMP takes advantage of the unibody motor/reducer structure to employ an oil cooling method. The E-GMP directly sprays a mist of cooling/lubricating oil using Electric Oil Pump(EOP) onto the coil inside the motor to more effectively dissipate heat.
Finally, the power semiconductor on the inverter power module – which controls the rear-wheel motor – is upgraded for a 5% increase in range. Ordinary inverter power modules use silicon (Si) power semiconductors; the E-GMP’s inverter power modules are equipped with more durable and efficient silicon carbide (SiC) power semiconductors to maximize efficiency.
The E-GMP boasts the world’s first multi-charging system that can accommodate either 800V or 400V charging without the need for any manual adjustment.
The new PE system also remarkably improves E-GMP’s charging speed and convenience. The most obvious change is that 800V ultrafast charging is now the default option. A radical upgrade from mainstream 400V charging, this high-voltage charging method charges a battery to 80% in just 18 minutes, compared to the 30-to-60 minutes needed by conventional 400V chargers. Granted, some new BEVs are capable of charging to 80% in 20+ minutes with 800V charging, but even that is a respectable upgrade. The E-GMP’s 800V high-speed charging requires only 5 minutes to deliver 100 kilometers in driving distance – immediately placing it among the world’s best for charging speed and convenience.
But E-GMP’s convenience is not only a product of its rapid charging speed. BEVs based on the E-GMP not only support 800V high-speed charging – as yet unsupported by many BEV infrastructures – but also mainstream 400V fast charging. Those BEVs on the market which currently support 800V charging predominantly offer the same functionality but require an additional adapter to shift between the two charging methods. On the contrary, the E-GMP boasts the world’s first multi-charging system that can accommodate either 800V or 400V charging without the need for an additional adapter. This hassle-free innovation stems from Hyundai Motor Group’s patented technology for boost conversion, whereby the charge from a 400V source is boost-converted into 800V by the rear motor and the inverter before it reaches the battery.
Batteries in the E-GMP can also double as a high-capacity external power bank.
Batteries in the E-GMP can also double as a high-capacity external power bank. Existing BEVs only allow one-directional charging: the transfer of power from an external source to the vehicle battery. But the E-GMP comes with the hassle-free V2L (vehicle-to-load) function, which allows the passenger to charge external devices with the vehicle battery without an additional adapter. This function was made possible through the Integrated Charging Control Unit (ICCU), which controls built-in bi-directional chargers, and the Vehicle Charging Management System (VCMS).
The V2L function’s maximum power output is 3.5kW. This is more than the Korean Electric Power Corporation’s 3kW default household power output contract, a predictive measure of the amount of electricity used in one month. This should sufficiently meet all the needs of consumers on-the-go. BEVs based on the E-GMP, in effect, become “traveling” charging stations for 220V slow-charging appliances, as well as for power-hungry camping equipment. During emergencies, it can serve as a power bank for other essential devices as well. E-GMP BEVs can even slow-charge the batteries of other BEVs through the ICCB (In-Cable Control Box), essentially a portable charger.
The E-GMP is structurally different from existing ICEV platforms, manifesting itself in important design advantages, inside and out.
The E-GMP is structurally different from existing ICEV platforms, a difference that manifests itself in important design advantages, both for the exterior and interior. The biggest difference is that the E-GMP omits the bulky engine and driveshaft of an ICEV. The space formerly occupied by the engine is instead occupied by the low-volume PE system; the car body floor is occupied by the heaviest part of a BEV, the battery. Due to these changes, the physical proportions of E-GMP BEVs can appear quite different too, generally allowing for more effective use of space. Specifically, the wheelbase (the distance between the front and rear axles) and the overhangs (the distances between the center of the front/rear axles and the front/rear bumpers, respectively) have undergone significant changes.
With the engine room’s volume drastically reduced, the front overhang has shortened; the bonnet now falls more sharply, with the cowl point (where the windshield meets the hood) pushed forward. The wheelbase, on the other hand, has become longer, resulting in drastically different proportions as illustrated below:
These structural differences have significant positive effects on cabin space. The longer wheelbase means more legroom. Removing the driveshaft also allows for a completely flat floor, meaning seats can be placed anywhere that matches the particular lifestyle needs of the consumer.
There are even more space advantages unique to the E-GMP: the climate control system inside the cabin dashboard has been moved to the space formerly given over to the engine bay. This shrinks the dashboard volume and realizes a “slim cockpit” design. Passengers in the front seats can therefore enjoy a more spacious and comfortable environment than they would in a BEV based on an existing one.
Thanks to its low-center-of-gravity design, BEVs based on the E-GMP demonstrate stellar driving performance across acceleration, cornering, and ride comfort – regardless of segment.
E-GMP’s structural design also maximizes performance. The aforementioned battery is the key factor. As the heaviest part of a BEV, placing it low at the center of the car body gives the vehicle a low-center-of-gravity design. Placed between the axles, the battery concentrates the vehicle’s weight in the lower half of the body and effectively distributes weight to increase handling performance. Indeed, BEVs based on the E-GMP demonstrate stellar acceleration, cornering, and ride quality, regardless of the segment.
The newly developed suspension further adds to these performance increases. The five-link rear suspension comes links the wheels to the body through five links to absorb vertical and lateral shocks and improve maneuverability. The rear suspension structure and subframe (the suspension’s basic skeleton) were also integrated with the built-in PE system; this modularization further improves on-road performance.
The E-GMP also features its special integrated drive axle (IDA), the first mass-produced IDA in the world, developed by Hyundai Motor Group early last year. Previously, the driveshaft and the wheel bearing were connected separately, like nuts and bolts, to deliver power from the engine or motor to the wheels. However, the IDA integrates these two parts into one and no longer requires a separate connection. As a result, stiffness is increased by 42%, while weight is reduced by 10%. These improvements directly lead to better handling and ride quality for BEVs based on the E-GMP.
Many of the E-GMP’s structural changes are safety-minded.
Many of the E-GMP’s structural changes are also safety-minded. Using the space made available in the front of the vehicle (thanks to the omission of an internal combustion engine), the engineers have applied frame and subframe reinforcements that form a multi-skeletal structure. This structure more effectively distributes and absorbs the collision energy of an impact, and minimize the energy delivered to vehicle occupants and the battery. The rear structure receives similar changes: a shock-absorbing frame is installed near the bumper, dispersing the energy of a rear impact. To further protect the rear wheels and, above all, occupants in the cabin, heavy reinforcements to the body further minimize deformations from external shocks.
The physical structures at the center of the body also provide significant protection for the battery and PE system. The side sills feature extruded aluminum reinforcements to shield the battery from lateral shocks. In addition, the horizontal crossmember inside the vehicle floor is constructed from ultra-high strength steel plates normally reserved for hot-stamped parts.
Naturally, it’s also important that the battery is held fixed in its place during an accident. To that end, the Group’s engineers have employed a so-called ‘battery-penetrative’ mounting method. This secures the battery to the car floor with eight long bolts, which penetrate the lower edge of the battery. This not only maximizes the sturdiness of the battery-to-floor connection but also improves the physical stability of the battery in the case of an external shock. This method also improves the vehicle’s NVH (noise, vibration and harshness) performance by reducing any vibration movements of the battery under normal use.