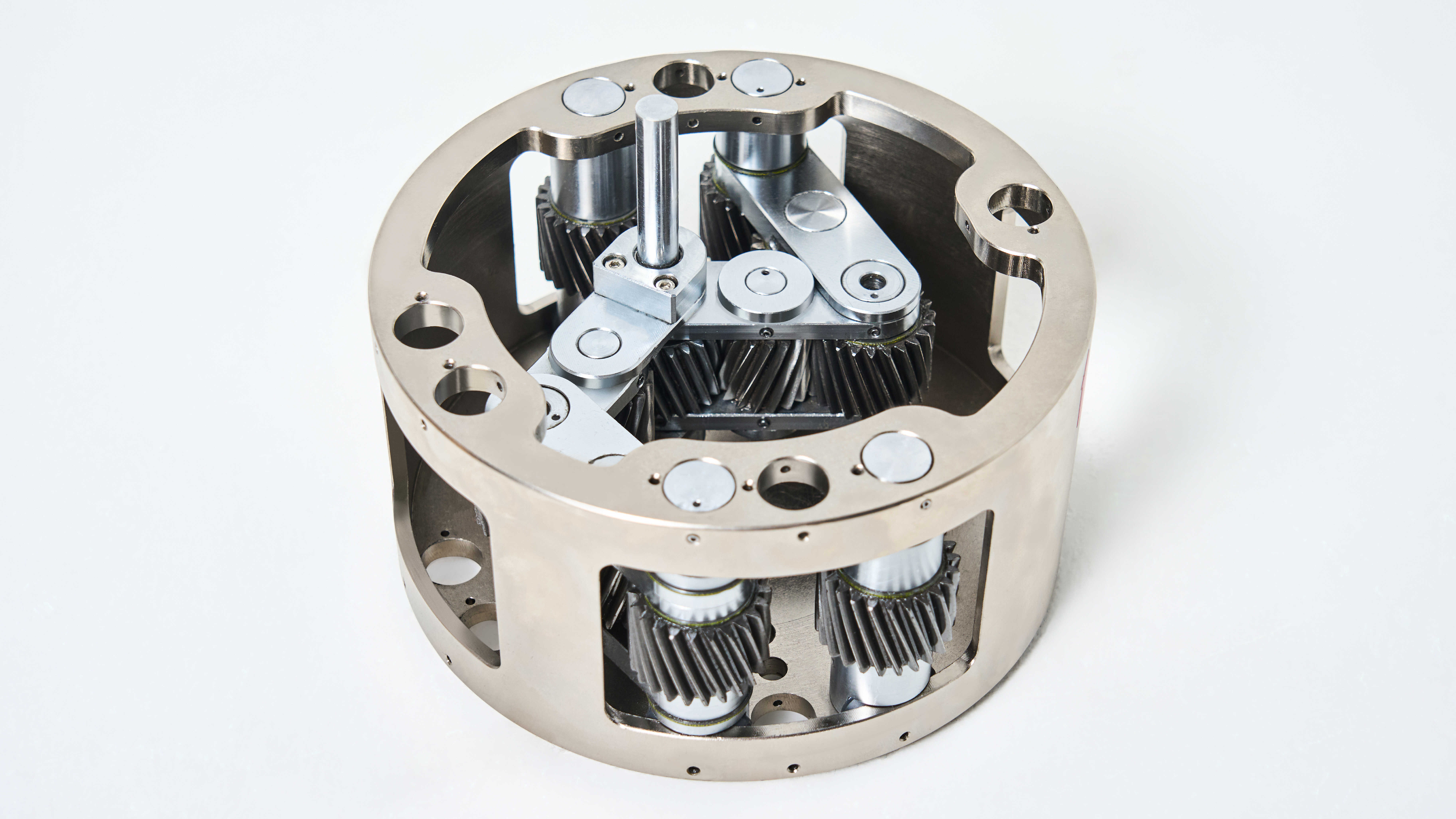
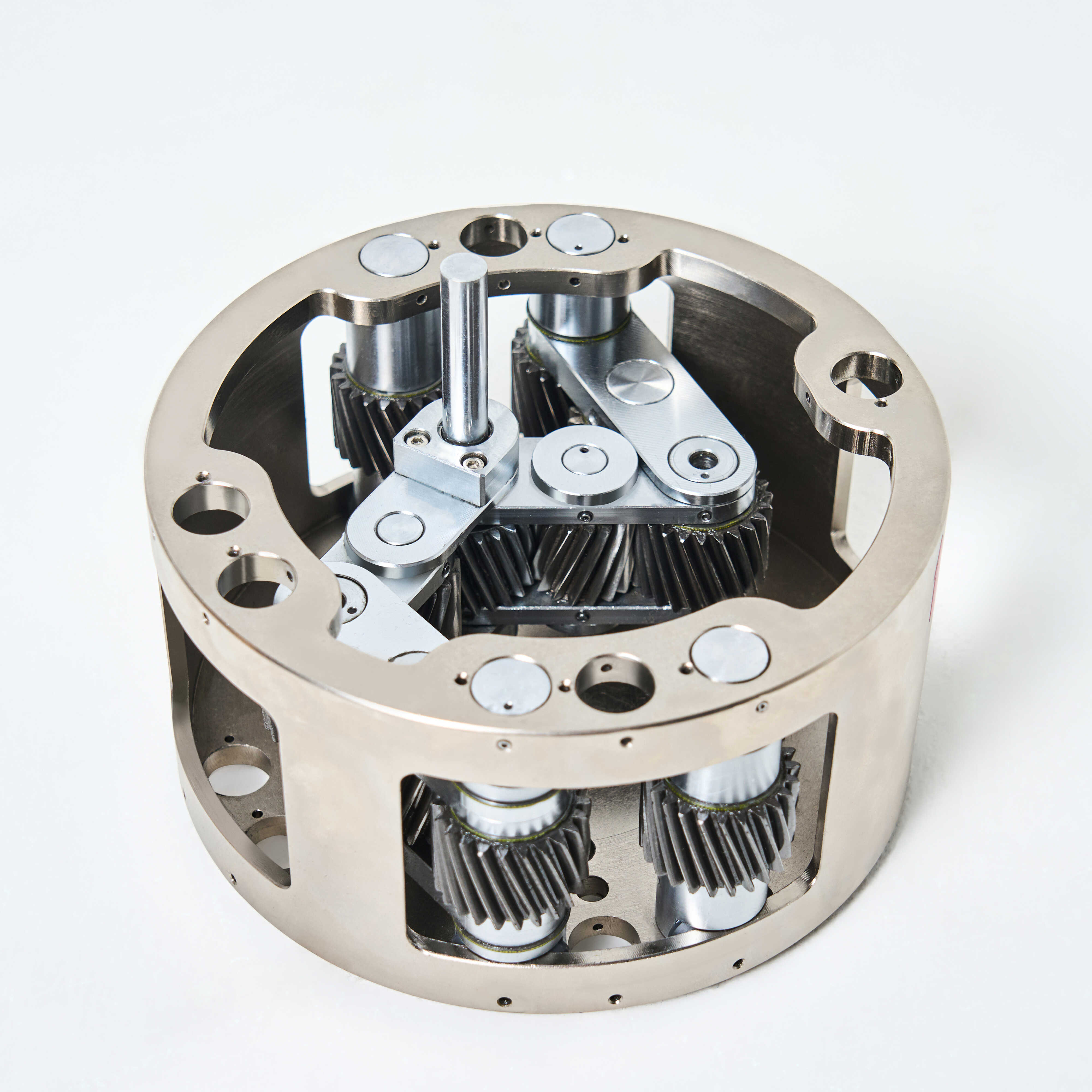
2023.12.04 Hyundai Motor Group
The true innovation of the electric vehicle era lies in the increased freedom to manufacture cars. As is well known, electric vehicles have simpler drivetrains than vehicles with internal combustion engines. This allows for the free arrangement of the essential parts of the vehicle, greatly increasing the interior space. A case in point is the spacious interior, a key feature of electric vehicles utilizing Hyundai Motor Group’s electric vehicle platform, E-GMP.
Hyundai Motor Group won’t stop here, and is preparing for a better future. Going one step further from a dedicated platform optimized for electric vehicles, the group is attempting to innovate the wheel drive system itself. By miniaturizing or repositioning the wheel drive system, which is a large part of the underbody of an electric vehicle, more interior space can be freed up. These technologies, along with PBVs that configure spaces in accordance with the user’s purpose, are essential for the future of mobility.
The Universal Wheel Drive System (“Uni Wheel”), being developed by Hyundai Motor Group’s Institute of Advanced Technology Development (IATD), is a new wheel drive system for the future mobility era. The planetary gear structure of the Uni Wheel creates a reducer-like effect and is directly connected to the drive motor without a constant velocity joint, allowing for expanded interior space.
Most of Hyundai Motor Group’s current electric vehicles use the “e-Axle,” an integrated drive module that combines a drive motor, inverter, reducer, differential device, etc. The integrated drive module in these electric vehicles takes up less space than an internal combustion engine, allowing for an expansion in interior space. However, if the vehicle is configured using the Uni Wheel, the reducer goes inside the drive wheel, and the drive motor moves right next to the wheel, freeing up more interior space.
The Uni Wheel is made up of planetary gears. In the center is the sun gear, which transmits power from the drive motor, and on the outside is the ring gear, which turns the wheel. In between is the linkage, which is two sets of four pinion gears connected together. When the drive motor moves the sun gear, the rotational force is transmitted to the outer ring gear through the linkage, and the ring gear turns the wheel. This configuration allows the Uni Wheel to transfer power seamlessly and with nearly the same efficiency regardless of the wheel’s up and down motion. This means that it’s possible to drive even if the central axis of the motor and the central axis of the wheel do not match. Kim Ki-seok, a senior researcher at Hyundai Motor Group’s IATD, explained the advantages of the Uni Wheel.
“The Uni Wheel will bring about a greater change than the shift from internal combustion engine vehicles to electric vehicles. When you apply the Uni Wheel, the constant velocity joint and driveshaft that were connected to the e-Axle reducer disappear. What’s more, you can change the arrangement of the motor/reducer/inverter, which was centered between the two wheels. It becomes possible to create new space by pushing the drivetrain toward the wheels, something we’ve only ever dreamed about.”
This isn’t the only advantage of the Uni Wheel. By leveraging the ability to drive even when the central axis of the motor and the central axis of the wheel aren’t aligned, the minimum ground clearance can be adjusted to suit the road surface or driving conditions to improve safety or efficiency. It becomes possible to raise the minimum ground clearance on rough roads to prevent damage to the body of the vehicle, and lower the minimum ground clearance at higher speeds to increase fuel economy (by reducing drag).
The ability to generate more power from the same motor is also a key feature of the Uni Wheel. “The Uni Wheel can create different reduction ratios, from 6 to 10, depending on the gear combination. It can deliver 6 to 10 times more torque to the wheels than a drive motor can deliver. It’s definitely possible to create a system with a higher or lower reduction ratio as needed,” explains Min Kyeong-cheol, a senior researcher at IATD.
The Uni Wheel also has advantages in terms of durability and ride quality. While driving, the body of the vehicle will experience an impact of 0.7G or less, and the wheels will experience an impact of 6G or more. Because the Uni Wheel mounts the motor to the body of the vehicle rather than inside the wheel, there is less impact on the motor, which results in increased durability. Due to its structure, the Uni Wheel also takes on part of the role of suspension to absorb road bumps. This also helps improve the ride quality.
Furthermore, the Uni Wheel is light and sturdy. Researchers optimized the size and thickness of each gear to meet the vehicle’s required up and down range of motion, and used structural analysis to reduce weight. In other words, it was refined into an optimal shape considering both durability and weight reduction.
Lim Woo-hyun, a senior researcher at IATD, explained the durability of the Uni Wheel. “To achieve high performance in a small structure, durability is essential. The Uni Wheel has secured reliability by using materials and heat treatment technologies that have been proven through mass production of transmissions. In addition, optimized design through strength analysis ensures trouble-free operation under normal driving conditions. It can handle even cars driving at 260 kilometers per hour.”
The Uni Wheel is an original wheel drive system developed by Hyundai Motor Group’s IATD. Because the Uni Wheel has a different structure compared to a typical drivetrain, Hyundai Motor Group’s IATD had to pave the way for its development. Even simply explaining the concept to other researchers was difficult, as there was no technology to use as an example. Senior Fellow Park Jong-sool of IATD, who led the development of the Uni Wheel, says that a lot of work went into the development of the Uni Wheel, as well as the research and testing process.
“The hardest part was finding a structure that didn’t change the relative phase of the sun gear. In the early stages of development, we had a lot of concerns as we didn’t even know if there was a structure that wasn’t affected by the up-and-down motion of the wheel. When the pressure of failure got to me, I would talk to my colleagues and gain strength. Validation testing was also a challenge as there were no example cases to reference. There were many methods, but we decided to test different specifications by changing the mounting position of the gears on one carrier and analyze the advantages and disadvantages. We set the arrangement of the gears in the shape of the letter ‘N’ or ‘W,’ and compared the advantages and disadvantages of four different specifications with different sizes and angles of the gears to find the optimal configuration. The results of this showed that the ‘W’ structure had unstable output characteristics because the shape was symmetrical but the operating force was not.”
New technologies need to be tried and tested to prove themselves. This is how the Uni Wheel was perfected, as various enhancements were made during this development and validation testing process. For example, when the researchers found welding defects during assembly after prototyping, they didn’t see them as a simple mistake. In order to eliminate the possibility of welding defects and to improve the perfection of the Uni Wheel, several prototypes were prepared with different laser welding conditions. The welding surfaces of each prototype were then cut and inspected to determine the final welding specifications. Lee Dae-in, a senior researcher at IATD, explained that this meticulous preparation, checking, and reinforcing work is what makes the Uni Wheel so perfect.
“For the carrier, which is one of the important parts of the Uni Wheel, we used structural analysis to identify weak areas in advance and address potential structural problems through design changes to ensure the structural rigidity of the prototype in advance. We were worried because it was our first time doing structural analysis, but after attaching gauges to measure the stress in key areas during the test, we were able to put our minds at ease.”
Senior Researcher Lee Yeo-hae of IATD, who is developing the cooling method of the Uni Wheel, added her own explanation. “We’re working on an oil circulation structure for the next development specification, and are designing a lubrication system through flow analysis. It would be easy to fill the inside of the Uni Wheel with oil, but oil doesn’t reach each bearing with this method. Therefore, we’re developing oil holes in the shaft so that oil can be supplied directly to the bearings, and are reviewing the flow distribution analysis so that each part doesn’t end up having too much or too little oil.”
Thanks to these various efforts, the Uni Wheel has now successfully completed the structural, strength, and transfer efficiency tests that need to be performed for wheel drive systems. Suspension operation is currently being tested, and in 2024, detailed target testing will be conducted for vehicle development. The current product being tested is a rear-wheel-based system, but depending on the results, the group also plans to develop the Uni Wheel for front-wheel application. The Uni Wheel is expected to significantly increase steering stability by implementing torque vectoring control based on a structure that enables independent drive of the left and right wheels.
The Uni Wheel enables the use of an interior space even between the wheels, and its small motor can stably generate a large amount of power, making it suitable for a variety of mobility applications. In addition to this, its modular design allows it to be applied to wheels ranging from 4 inches to more than 25 inches, so it is expected to be used not only for eco-friendly vehicles like electric vehicles and hydrogen fuel cell vehicles, but also for small mobility like delivery robots and electric wheelchairs. Senior Fellow Park Jong-sool explained this versatility of the Uni Wheel.
“The Uni Wheel’s freely adjustable minimum ground clearance makes it possible even to travel down stairs without wobbling. It may also be a breakthrough technology to help the mobility-impaired. Like this, the Uni Wheel is a completely new wheel drive system based on this unique idea. In recognition of its innovation, it won the top prize at Invention Day 2022, and this year, it was patented in both South Korea and the United States. There are still many technical barriers to overcome before mass production, but everyone working on the Uni Wheel is committed to making it happen.”
The Uni Wheel is not just a drive system to make electric vehicles more marketable. In fact, it’s a technology that encompasses all modes of mobility, from current mobility, including electric vehicles and hydrogen fuel cell vehicles, to up-and-coming small mobility, such as PBVs, delivery robots, electric wheelchairs, and more. As Hyundai Motor Group strives to realize mobility for a better world and a better future, the group looks forward to seeing how new technologies will change our lives.
Images. Cho Hyuk-su
[Op-ed] Robots Jump into the Mobility Industry
2021.01.21 19min read