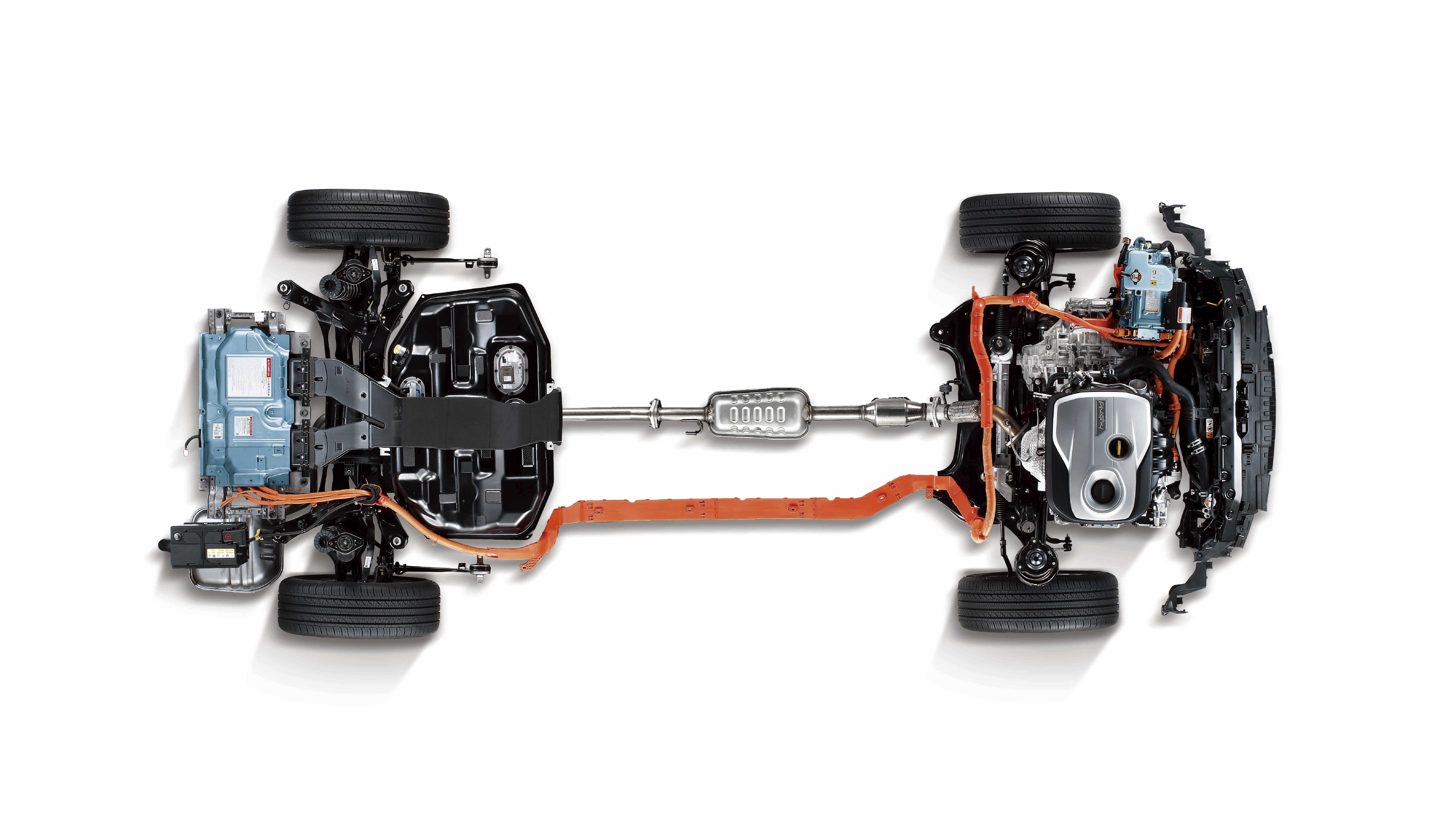
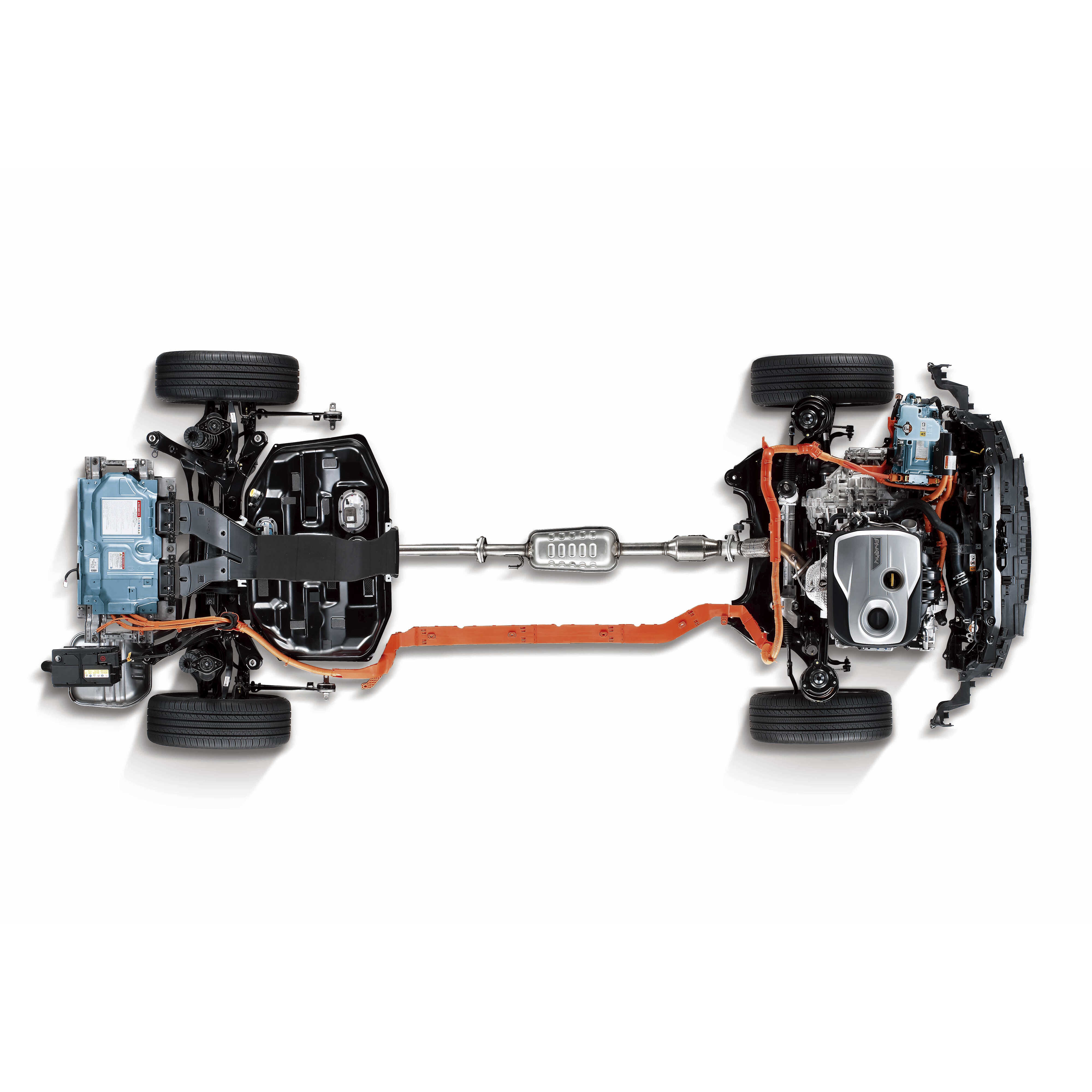
2024.06.21 Hyundai Motor Group
The word, hybrid, means “a mixture of elements of different properties,” and is used in many different industries. One of the most well-known examples of this is the hybrid vehicle. A hybrid vehicle combines an internal combustion engine with a drive motor to achieve both power and fuel efficiency and is becoming more popular than ever in the era of electrification. In the last three years, hybrid vehicles have been at the top of the rankings of popular vehicles in Korea. This is a testament to the fact that there is still ample demand from people who are familiar with internal combustion engines.
HMG has been developing hybrid technologies for decades, building a solid portfolio and garnering attention from major global media outlets. For example, Hyundai Tucson Hybrid and Elantra (Avante) Hybrid were recognized by U.S. News & World Report’s 2022 Best Cars for the Money awards as “Best Hybrid/Electric SUV” and “Best Hybrid/Electric Car” respectively, one of the main categories of the awards. In addition, Edmunds, a U.S. automotive media outlet, selected Kia Sportage Hybrid as the Top Rated SUV 2024, recognizing HMG’s hybrid technology as world-class.
The development of HMG’s proprietary hybrid system, however, was about as easy as finding a needle in a haystack. It had been a race against the clock to stay ahead of other automakers who had taken the lead in hybrid technology. We spoke to Vice President Yong-seok Kim of the eP Test Group 2 and Part Leader Jae-won Ha of the Electric Drive Design Team, who were both there since the beginning of the R&D process, to hear some stories. Vice President Kim has been involved in the highs and lows of research and development of electrification technology since the early days. His challenges have resulted in not only the development of Korea’s first full hybrid system but also the world’s best charging performance and efficiency of today’s electric vehicles. Meanwhile, Part Leader Ha has been involved in the development of drive motors, a key component in HMG’s early hybrid models (Accent (Verna), Pride, Elantra (Avante), Forte, etc.) as well as Sonata and K5 hybrids, which featured the world’s first parallel full hybrid system, contributing to establishing proprietary technology.
In 2004, 33 research engineers gathered in the newly opened Hybrid Development Center at the Namyang R&D Center. They came together from their respective fields for one reason – to develop HMG’s own hybrid system. In order to pioneer a new path that had never been traveled before, these research engineers gave up going home for the night and stayed up late for research, purely fueled with their passion. Vice President Kim recalled that time. “Everyone put their lives on the line for this research. These were people who had been working hard in their own departments, as the so-called ‘best,’ and they all came together with a passion toward the same goal.” He likened the research engineers in the early days of hybrid vehicle development to the 33 Korean patriots who signed the Korean Declaration of Independence during the Japanese occupation, calling them “modern-day independence activists.” This was a tribute to the research engineers who “fought against” the Japanese automobile manufacturers that had a practical monopoly on hybrid technology and worked to develop their own technology.
HMG first became interested in hybrid vehicles in the 1990s. The need for eco-friendly vehicles grew as calls to address global environmental issues grew louder. In particular, the adoption of the Kyoto Protocol at the Third Conference of the Parties to the United Nations Framework Convention on Climate Change held in Kyoto, Japan in 1997 put the automobile industry on a-lert. The Kyoto Protocol states that greenhouse gas emissions must be reduced by an average of 5.2% from 2008 to 2010 compared to 1990 levels. This heralded stricter regulations on automobile emissions starting in 2005, and automobile manufacturers had 10 years to develop vehicles that meet these standards.
Accordingly, HMG was sketching out the outlines of a full-scale mass-production hybrid vehicle. At the 1st Seoul Motor Show in 1995, HMG introduced its first hybrid concept car, FGV-1 (Future Green Vehicle-1), based on Hyundai Pro Accent. According to Vice President Kim, HMG’s development of hybrid vehicles was a choice to respond to market changes. “For decades, countries around the world have taken steps to reduce the carbon dioxide emitted by cars to protect the environment, and regulations have been getting tighter year by year, forcing automobile manufacturers to respond in their own ways. We have also been intensely developing hybrid vehicles to respond to this trend and the demands of the global market.”
HMG saw the potential for hybrid vehicles through advanced development. It developed Accent (Verna) Hybrid and County Hybrid in 2000, and in 2004, Getz (Click) Hybrid, which took 16 months to complete, was produced in a limited run of 50 vehicles for government agencies. Getz (Click) Hybrid was a mild hybrid model with a drive motor assisting the engine and achieved 18 km/L fuel efficiency with a motor and inverter from Hitachi, with whom HMG had a technology partnership at the time, and a nickel-metal hydride battery from Panasonic.
After Getz (Click) Hybrid, HMG also unveiled hybrid models based on Accent (Verna) and Pride. While none of these three models made it to full-scale mass production, the development of these hybrid vehicles was an opportunity to clearly identify technical limitations. HMG recognized that its hybrid vehicles fell short of other manufacturers’ hybrids in terms of fuel efficiency, which is considered the core of a hybrid.
Vice President Kim recalled that the challenge was very lonely and difficult, starting with a lot of distrust. “No one believed that we could do it on our own. Overcoming being told to go to Japan or Germany to learn the technology or being told that fools rush in where angels fear to tread was harder than actually developing the technology. But we didn’t let that stop us – we encouraged each other, and we did our job.”
Mass production of hybrid cars in the mid-2000s was another problem to face. As the Korean hybrid vehicle market was not yet established, it was foreseen that the number of sales would be limited and that it would be difficult to recover development costs through sales revenue accordingly. In other words, HMG had to find a way to minimize cost losses while achieving the development goal of “vehicles with differentiated value.” In addition, the goal was to have lower consumer maintenance costs compared to gasoline and diesel for initial market entry.
After many long meetings, the consensus was to develop a hybrid system based on the already mass-produced LPi engine. HMG’s LPi engine offered both the practical aspects of eco-friendly performance and low maintenance costs. The Hybrid Center completed its own hybrid system based on this engine, and in July 2009, introduced Elantra (Avante) LPi Hybrid and Forte LPi Hybrid.
Elantra (Avante) and Forte LPi hybrids were very significant hybrid models that were both designed in-house and produced in Korea. HMG designed the core components such as motors, batteries, inverters, converters, and controllers in-house and successfully produced them in Korea rather than importing them to reduce production costs, leading to mass production for the public. What’s more, among the core components, the battery was the first in the world to use lithium-ion batteries in a mass-produced car instead of nickel-metal hydride batteries, which was a stand-out advantage.
*LPi engine: A liquid injection LPG engine that uses liquefied LPG mixed with air to feed the combustion chamber. It overcomes the shortcomings of existing LPG engines to deliver improved performance, superior fuel efficiency and low emissions, and solve starting problems in the winter.
After confirming the possibility of mass production with Elantra (Avante) LPi Hybrid and Forte LPi Hybrid, HMG began its march toward its final destination: a full hybrid system. In order to be competitive in the Korean and global markets, a full hybrid model with a motor that moves the vehicle directly depending on the situation and optimizes efficiency was essential, and it was also judged that it would only be possible to compete with other automakers by securing proprietary technology in a full hybrid system that could be driven by the drive motor alone. HMG could not simply copy Toyota’s series-parallel hybrid system, which was dominant in the hybrid market at the time. What’s more, Toyota already owned many of the relevant patents. During the development process, Toyota offered to provide technology and components, but HMG rejected this offer as it would have resulted in technology lock-in and would have made it impossible to lead the way in future hybrid vehicles.
HMG then began researching new technology methods again to perfect its own full hybrid system. The direction of development was decided to be a parallel full hybrid system (TMED, Transmission Mounted Electric Device) that could utilize HMG’s powertrain while being differentiated from other manufacturers. After deciding on a system approach, HMG sought cooperation with overseas companies to develop core components such as motors and inverters, but they were either too uncooperative or presented exorbitant costs during the development process, which ultimately ended without results.
The collaborations fell through, and the project once again lost its way. However, they couldn’t stop here, and the research engineers were reminded by what they had accomplished that “they could do it on their own.” The various attempts at the world’s first system had already produced excellent results, and this DNA of success instilled confidence in the hearts of the developers. Part Leader Ha, who was involved in the development of the drive motor for mild and full hybrid systems, explained the situation at the time.
“Elantra (Avante) LPi Hybrid is equipped with a drive motor designed in-house, which we used as a basis for designing a drive motor for the full hybrid. However, there were two main technical challenges to overcome. The first was the need for a more compact design due to the increased power output, and the second was the need to improve cooling performance due to the increased heat generation. To solve this problem, we designed the motor to be integrated with the transmission to maximize space utilization. We also adopted an oil cooling system using transmission oil to improve cooling performance. However, there was also a problem that the high temperature of the transmission oil changed the composition of the bond that held the permanent magnets inside the motor rotor core, reducing the holding power. This caused the motor to break inside and burn out at high voltages, so we solved this problem by filling the space around the magnets with non-magnetic materials. We then went on to develop the first motor that was directly exposed to transmission oil and conducted various validation tests on the material, which allowed us to mature technologically once again.”
The development of the drive motor, a core component of the full hybrid system, was successful, but problems arose in the design for mounting it. The development process was a continuous series of difficulties, as solving one problem led to another appearing. Part Leader Ha recounted the situation at the time.
“We needed to find additional space to mount the drive motor between the engine and the automatic transmission, so we decided to remove the torque converter and replace it with a wet engine clutch. We were able to secure space for mounting the engine clutch inside the drive motor rotor. The problem of shift shock was overcome by developing engine clutch engagement control technology. In a full hybrid system, if the engine clutch breaks, there is no place to create hydraulic pressure. After careful consideration, we solved this problem by adding an electric oil pump. The electric oil pump provides flow when the motor is running, and the clutch is engaged while driving.”
Part Leader Ha explained the advantages of the parallel full hybrid system. “HMG’s full hybrid consists of an engine, engine clutch, drive motor, and automatic transmission. Plus, the engine is equipped with an HSG (starter generator), so when driving in EV mode, the engine clutch disconnects the engine and drive motor, and the engine runs on the drive motor alone. When switching to HEV mode, the HSG wakes up the engine, synchronizes the rotational speed, and connects the engine and drive motor with the engine clutch. Ours is a parallel hybrid system with a regular transmission, whereas unlike this, Toyota uses a power-split hybrid system with planetary gears. Thanks to this structural difference, our system was able to realize fast response, excellent starting performance, and dynamic drivability. In addition, the transmission efficiency in EV mode is better, and the maximum speed in EV mode is also superior. In HEV mode, it performs even better when driving at medium to high speeds or at constant speeds.”
In May 2011, HMG introduced Sonata Hybrid and K5 Hybrid, equipped with the world’s first parallel full hybrid system, to the world. Under the bonnet of these models is a Miller cycle engine with reduced *pumping loss and a proprietary drive motor. They are also equipped with a hybrid power control unit (HPCU) and battery to achieve a certified fuel efficiency of 21.0 km/L. To many people’s astonishment, this is better than Toyota Camry Hybrid (certified fuel efficiency of 19.7 km/L), which has been competitive in the global market.
* Pumping loss: In the pumping motion of a piston reciprocating in a cylinder, a portion of the energy generated by the explosion of a mixture of gases is consumed in the process of drawing in and discharging the mixture
Vice President Kim reflected on what was happening at the time. “As we continued our research, our capabilities matured to the point where we stopped needing to borrow technology from other manufacturers. In 2011, we were able to introduce Sonata Hybrid and K5 Hybrid to the world with our own technology. Sonata and K5 hybrids were developed by departing from the hybrid’s conventional emphasis on fuel efficiency and were designed to be fun and enjoyable to drive. To this end, we adopted a steptronic transmission and designed the engine clutch to be controlled. We also strived to provide the best fuel efficiency for customers who want fuel economy, while satisfying the needs of customers who want to enjoy driving by adding the feeling of shifting gears and accelerating and decelerating. This was followed by the development of a hybrid model with a DCT, which started the current hybrid trend toward fuel efficiency and driving fun. HMG transformed from a fast follower to a first mover. Although there were many disappointments along the way, we overcame difficulties and eventually succeeded. Most importantly, I think we were able to gain the belief and confidence that ‘we can do it too’.”
He also talked about the challenges of completing a new hybrid technology that did not exist anywhere in the world. “We needed proprietary software to control our own hardware that no other company had benchmarked. To develop this, we had to go on countless drives using other automakers’ vehicles and systems and use our imagination. We constantly asked ourselves questions like, ‘Why do they turn the engine on and off at this point? Why do they charge the battery this way?’ and pored over tons of papers and technical data. We also spent time in scorching Death Valley in the summer and frigid Alaska in the winter, driving enough miles to circle the world several times. Basically, we had to put in more time and effort than other companies to make our own hybrid system perform better.”
HMG is considered to be one of the key leaders of the current transformation of the automobile industry. It has proven itself by introducing a number of competitive electric models in the era of electrification. In addition to electrification, HMG is also showing great results in the field of SDV (Software Defined Vehicle), which is expected to become a pillar of future mobility.
As for why HMG has been able to achieve such rapid growth, Vice President Kim attributes it to “accepting challenges and not backing down when everyone else was worried.” He recalls that just a few years ago, many people around him were skeptical of HMG’s continued commitment to delivering high-quality electric vehicles. “When I go overseas, I’m often asked, ‘Where did you get your technology from?’ But our technology wasn’t perfected overnight. The hard work we put into developing hybrid technology is the foundation for the mass production of electric vehicles today. Our 20 years of research on electrification technology is now showing results. What’s more, the realization of the importance of ‘control’ technology in the process of developing hybrid technology led us to take an early step into the software field. Our experience developing software to control hybrid systems made us realize the importance of vehicle control systems. We built up our software development capabilities for vehicles early on and were able to lay the foundation to take on the challenge of SDVs.”
Lastly, we asked him about the future of hybrid vehicles in the automobile industry, which is expected to be dominated by electric vehicles. “The electrification system is important, but at the end of the day, we need to meet the needs of the customer. Even electric models aren’t all about just the electrification technology. A vehicle is a sum of many factors, including quietness, driving feel, convenience, price, etc., so we need to develop the overall marketability of vehicles to make them more competitive. I think hybrid vehicles will remain relevant for a long time if they have versatile appeal.”
Part Leader Ha hopes to see more hybrid systems in HMG models as they have clear advantages in terms of efficiency, power and eco-friendliness. “It would be best for the planet if everyone drove an electric vehicle, of course, but if a significant number of the gasoline and diesel-powered cars on the road today were replaced with hybrids, that would also be a great way to reduce emissions and pollution. I think more consumers would choose hybrids if the lineup of hybrid vehicles were expanded.”
As seen so far, HMG’s hybrid technology is the result of the sweat and hard work of many people. The process in which HMG’s research engineers devoted themselves to development day and night was an opportunity to lay the foundation for HMG’s electrification technology as well as for the research engineers to grow as individuals. HMG will continue to challenge and strive to be a leader in the future era of mobility.
Images. Hyuk-su Cho