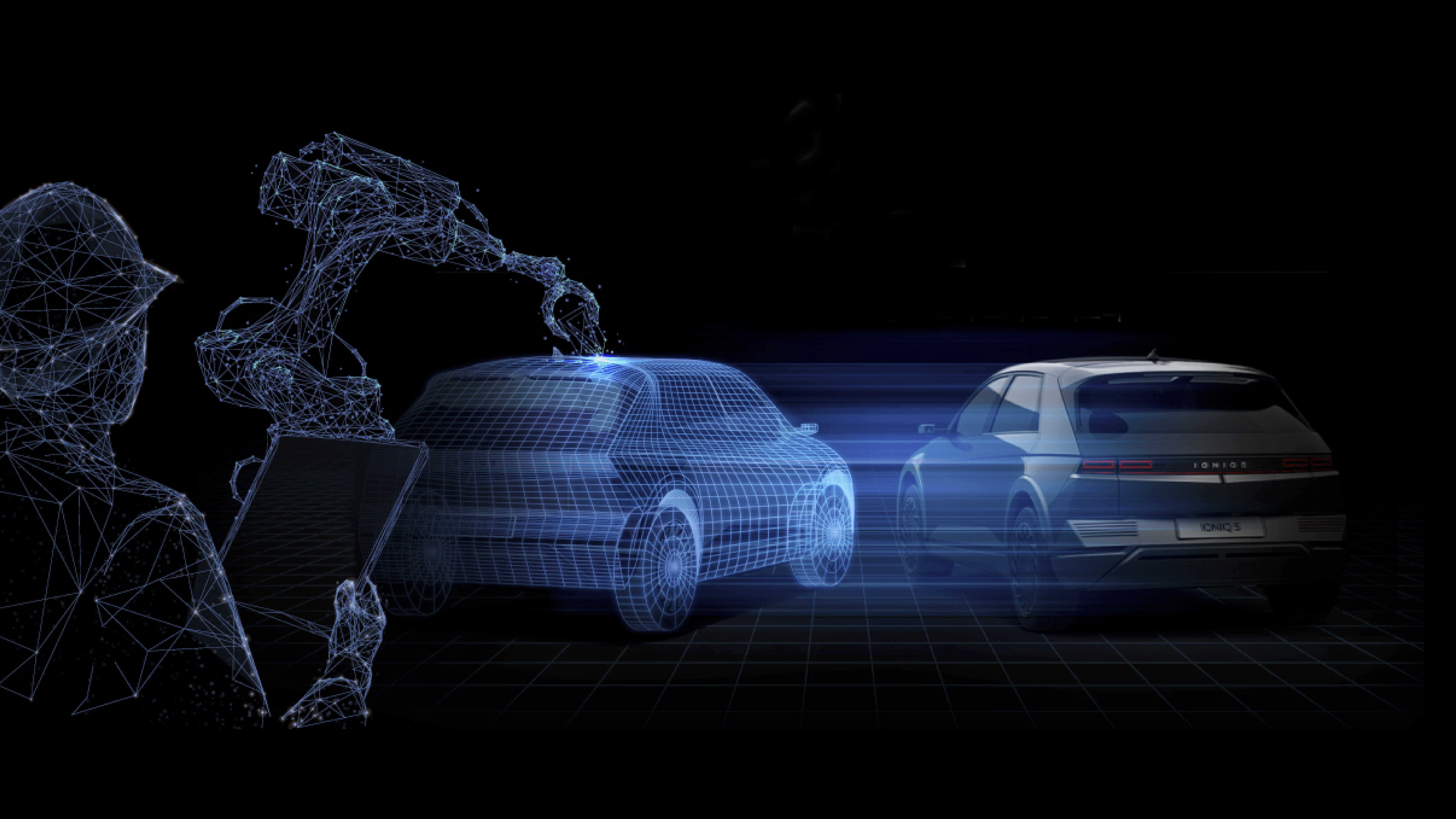
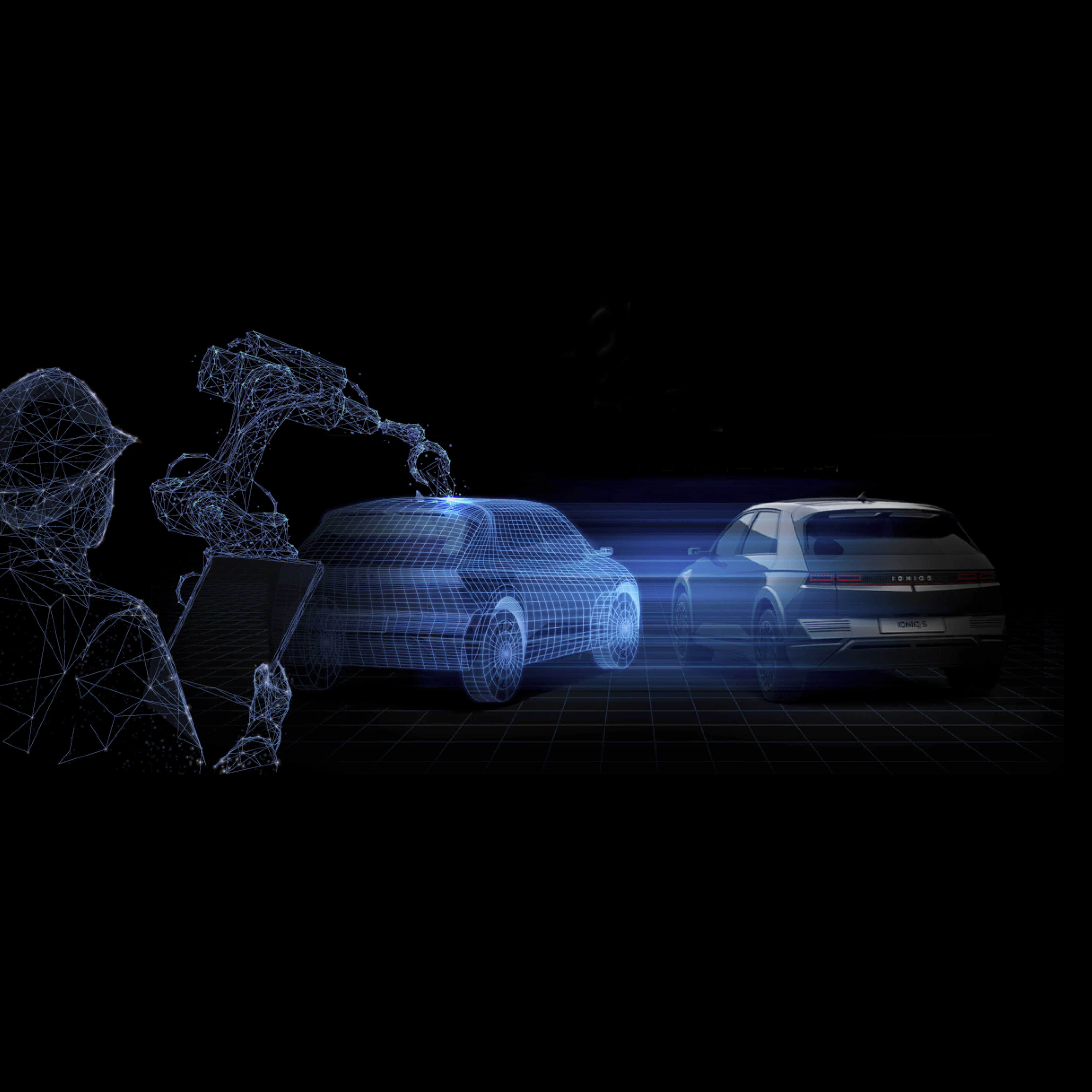
2024.06.19 Hyundai WIA
In April, Hyundai WIA participated in the SIMTOS 2024 exhibition, showcasing its 'Total Mobility Manufacturing Solution' specialized for electric vehicle manufacturing. This solution integrates Autonomous Mobile Robots (AMR), collaborative robots, and machine tools to manufacture electric vehicle components without human intervention.
During the exhibition, Hyundai WIA demonstrated the entire manufacturing process, from material transport to finished parts, using its Total Mobility Manufacturing Solution. AMRs transport materials, collaborative robots load them into machine tools, and once the work is completed, the robots transport the finished parts. This system is expected to bring significant changes to mobility production methods.
Using Hyundai WIA's Total Mobility Manufacturing Solution, it is possible to establish a manufacturing process that automates everything from part transport to final completion without human intervention through the integration of machines, robots, and intelligent control systems. Unlike traditional mass production methods using conveyors, this solution is advantageous for implementing multi-product small-lot production, which is beneficial in the era of diverse mobility, including PBVs (Purpose Built Vehicles).
As is well known, conveyor production methods are specialized for mass-producing a single product, meaning that extensive changes to the production line are necessary to manufacture different products. In contrast, the cell-based manufacturing solution introduced at Hyundai Motor Group's Singapore Global Innovation Center (HMGICS) uses multiple cells that independently perform all manufacturing processes required for product production, such as assembly, transport, and inspection. This allows for the production of a variety of products. Hyundai WIA's Total Mobility Manufacturing Solution follows this concept by automating the manufacture of diverse parts in one place.
AMRs used in Hyundai WIA's Total Mobility Manufacturing Solution perceive their surroundings, plan routes independently, and transport products. This allows for easy adaptation to changes in processes or logistics flow needed for diverse product production.
One of the core technologies of AMR is 'SLAM (Simultaneous Localization And Mapping).' Through camera or LiDAR observations, the robot autonomously determines its position, simultaneously creates a map of its surroundings, plans routes, and performs obstacle avoidance.
Efficient logistics control technology is crucial for managing multiple AMRs. This technology enables control of each robot's work schedule and transport process to ensure optimal routes, allowing robots to detect and avoid people and obstacles autonomously. Additionally, features for stable product transport are included. For example, the 1-ton AMR can lock the direction of the top platform and move only the bottom part to change direction, reducing shaking and radius when transporting long and heavy equipment.
Hyundai WIA's Total Mobility Manufacturing Solution can also reduce the burden on workers by assigning heavy material loading and transport tasks to robots. Unlike industrial robots, collaborative robots designed to work alongside humans can work together with people.
Industrial robots are used to automate tasks that humans cannot perform, such as welding heavy car bodies, and operate in separated areas with safety fences to prevent human access. In contrast, collaborative robots work in the same space as humans, assisting or replacing human tasks.
Safety is paramount for collaborative robots. Critical safety and collaboration technologies include direct teaching (a technique where the user directly programs the robot's path), force control, external force detection, and collision prevention. Hyundai WIA's collaborative robots can be set to stop immediately upon light contact with a person. These robots can handle weights ranging from 5 to 15 kg, making them capable of loading and unloading workpieces into machine tools in place of humans.
The performance of machine tools affects the ability to manufacture parts. Hyundai WIA's machine tools boast high productivity and precision optimized for automotive part processing. The tools maintain high precision even during long continuous processing through structural design that minimizes thermal displacement using proprietary structural analysis techniques. Various automation solutions, such as MPS (Multi Pallet System, which automatically replaces workpieces set in an external pallet box) and PLS (Pallet Line System, which automatically transports processed products using a line), can be applied.
At SIMTOS 2024, Hyundai WIA showcased the 9-axis multitasking machine XM2600ST and the cost-effective vertical machining center KF5, demonstrating the processing of eight types of electric vehicle-specific parts, including motor and converter components, battery cases, and lightweight wheels.
The XM2600ST features two spindles, a mill head, and a lower turret, allowing it to quickly and precisely process complex-shaped products with a single setup. The two spindles enable the second spindle to begin secondary processing immediately after the first spindle completes its task, significantly enhancing productivity. The mill head is equipped with a high-precision encoder with a resolution of 0.0001°, which detects very fine movements. This makes the XM2600ST ideal for advanced complex machining applications in fields requiring high precision, such as aerospace and medical components.
The vertical machining center KF5 is an upgraded model of the popular KF5600II, featuring enhanced structural stability. The KF5 offers a variety of options, providing excellent cost-performance. It includes various lineups and core units, such as columns and magazines, which are essential for machine tools. Since initial investment costs for machine tools are high, purchasing multiple products at once can be challenging during line design. However, the KF5 allows for cost-effective purchases by selecting only the necessary functions for the process. The KF5 can be used for machining a wide range of parts, including automotive knuckles, carriers, rack housings, small parts for general machinery, electronic components, and mold parts.
Automobiles have continuously evolved, especially over the past decade. Advanced driver assistance systems have quickly been applied to all models, hybrid systems have become essential powertrains, and electric vehicles have emerged as key players in the automotive market. These changes are not limited to the vehicles we experience daily; manufacturing processes have also undergone significant transformations.
Hyundai Motor Group has achieved production innovations through its Singapore Global Innovation Center, including cell production systems, intelligent automotive manufacturing platforms, and mobile robot deployment. Hyundai WIA's Autonomous Mobile Robots (AMRs) are central to this effort. These AMRs will be used in various global production bases, including the upcoming electric vehicle-dedicated plant, Metaplant America (HMGMA), in the United States. The Hyundai Motor Group is revolutionizing automotive production methods to make them more convenient and safer for humans, who are both the creators and users of automobiles.