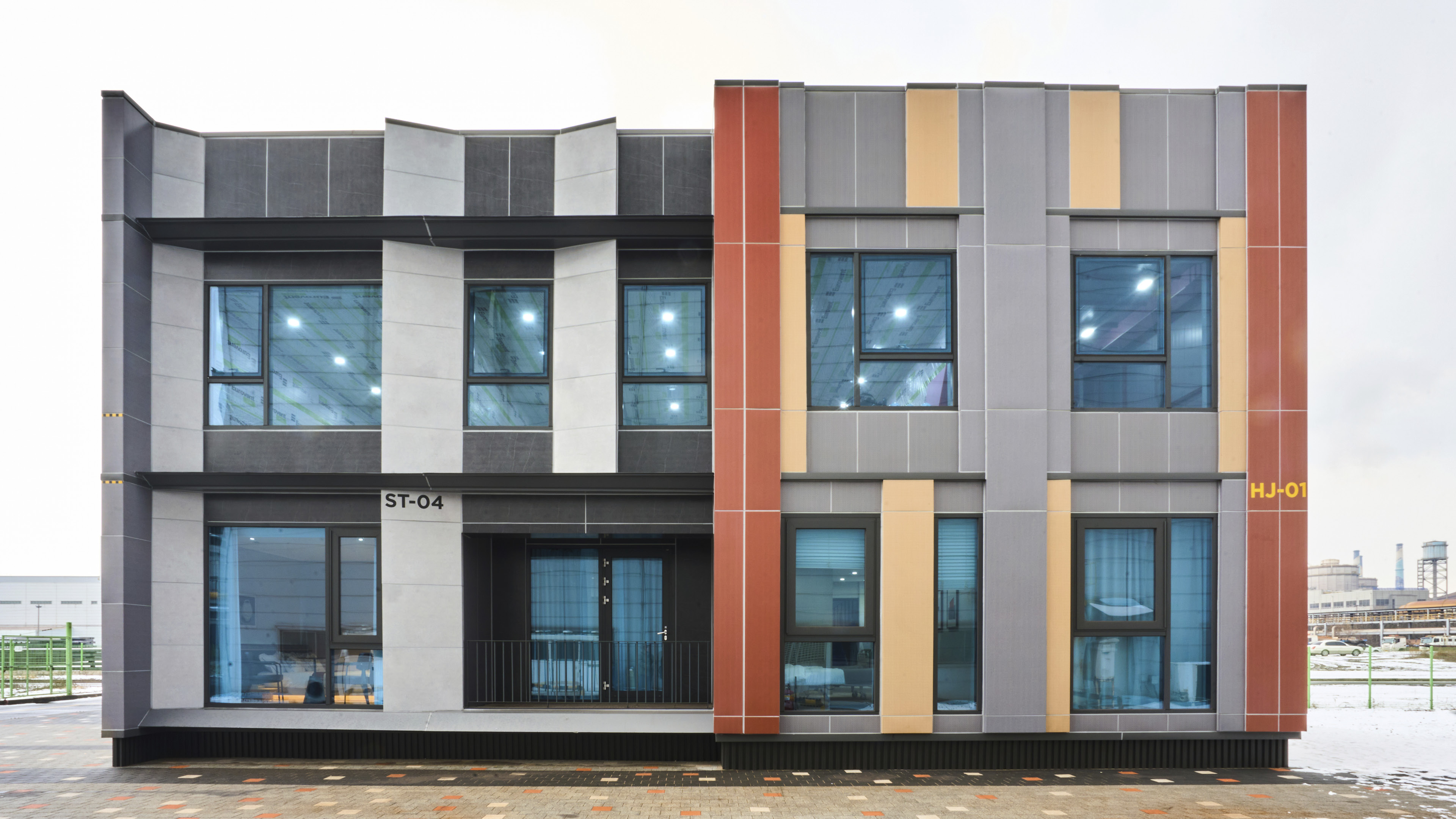
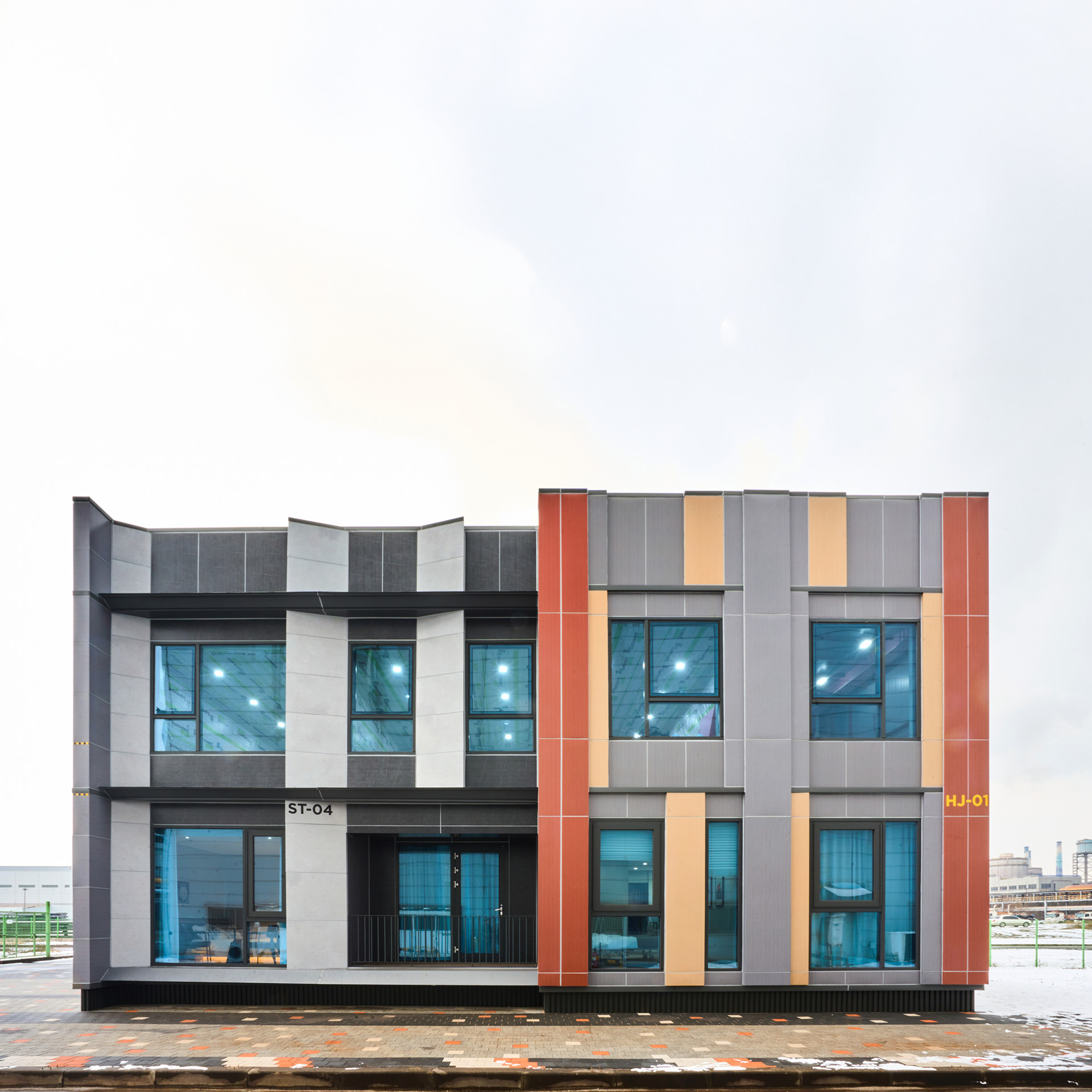
2025.02.28 Hyundai Motor Group
Architecture is a comprehensive art form that reflects the social, technological, and aesthetic currents of its time. As the spaces where we live and move, buildings must continuously adapt to evolving needs and trends. Just as a comparison between past and present apartment designs reveals how lifestyles have changed, so too have our expectations of architecture. Today’s buildings must incorporate factors such as livability, efficiency, and sustainability—key reasons why Hyundai Engineering has long recognized the potential of modular construction.
H-Modular Lab is a full-scale modular testing facility integrating advanced technology, jointly established by Hyundai Engineering and Hyundai Steel. Hyundai Engineering leads the modular construction industry, drawing on years of expertise, including the development of Korea’s tallest modular building (13 stories). Hyundai Steel, renowned for its expertise in construction-grade steel, enhances the partnership with exceptional product quality and technical innovation. The collaboration between these two industry leaders reinforces their shared vision, creating synergy in modular construction.
The modular construction method incorporates the mass production principles of manufacturing into architecture. Each module is a three-dimensional unit fully equipped with all essential building components, from its structural framework and finishes to furniture, plumbing, electricity, and communication systems. Unlike conventional methods, which require concrete to be poured on-site, modular construction assembles pre-manufactured modules at the construction site—much like stacking blocks.
Modular construction offers numerous advantages, including superior quality, enhanced safety, and reduced construction time. Since modules are produced in standardized formats, quality control is more precise and efficient. With over 70% of the construction process completed in a controlled factory environment, on-site labor requirements are significantly reduced, improving overall safety. Additionally, simultaneous work at both the modular production facility and the installation site accelerates project timelines by approximately 30–50%, making modular construction particularly advantageous for high-rise and large-scale developments. Furthermore, modular structures can be easily dismantled and relocated, providing greater flexibility to accommodate future demands and evolving site conditions. This approach enhances efficiency, promotes sustainability, and aligns with ESG-driven construction strategies.
The expansion of modular construction is inevitable. In preparation for this shift, H-Modular Lab serves as a testing ground for modular construction technologies at various scales, from low-rise buildings to high-rise structures. Here, Hyundai Engineering and Hyundai Steel conduct research and oversee the entire modular construction process, from design and fabrication to transportation and installation.
A closer look at H-Modular Lab from the outside reveals an interesting detail—all the modules forming its front façade are uniquely shaped. This highlights a key feature of modular construction: the flexibility to combine various modules as needed. In high-rise modular buildings, this approach enables a diverse mix of module types across floors, resulting in dynamic and visually distinctive exterior designs.
Each side of H-Modular Lab showcases a variety of patterns, ranging from marble and wood to stone and steel, demonstrating the versatility of printed steel plate technology. Creating intricate designs or decorative patterns with traditional materials like tile or marble typically requires extensive labor, high costs, and long construction timelines. Printed steel plates, however, provide a more efficient alternative, delivering the same aesthetic at a fraction of the cost while significantly reducing construction time.
Even the paving blocks at H-Modular Lab stand out—they incorporate Hyundai Steel’s steel slag technology. Rather than relying solely on natural aggregates, these blocks partially substitute them with steel slag, a byproduct of the steelmaking process. This replacement accounts for approximately 35–40% of the total aggregate weight, resulting in a final product that is stronger and more durable than standard concrete blocks.
Additionally, steel slag blocks can absorb carbon dioxide (CO₂) from the air. The calcium oxide (CaO) in steel slag reacts with atmospheric CO₂ to form calcium carbonate (CaCO₃), which fills microscopic gaps within the block. This process not only strengthens the structure but also improves durability by preventing the infiltration of external contaminants such as moisture, alkalis, and sulfates.
Each floor of H-Modular Lab serves a distinct purpose. While the second floor is dedicated to testing key modular performance technologies, such as inter-floor sound insulation and airtightness, the first floor functions as both an exhibition space showcasing the lab’s innovations and a display area featuring various modular applications, including hospital rooms, dormitory living quarters, and hotel suites.
Healthcare facilities are among the sectors that benefit most from modular construction. With its rapid-build capability, modular construction plays a crucial role in emergencies such as pandemics or wars, where the urgent expansion of medical infrastructure is essential. H-Modular Lab integrates printed steel panels for interior applications, demonstrating their practicality. In patient rooms, fabric-textured finishes have been chosen to create a warm, comforting environment while ensuring effortless maintenance. As a dry construction method, these fabric finishes also help reduce construction timelines, making them an ideal fit for modular architecture.
The dormitory at H-Modular Lab provides a significantly more comfortable environment compared to conventional accommodations. It highlights the core advantages of modular construction—rapid and efficient space creation—through a well-structured, highly functional interior layout, ensuring both practicality and comfort. Beyond dormitory rooms, the space can also be adapted for various purposes, such as shared living areas and educational facilities.
The hotel module demonstrates the potential of modular construction in creating high-end spaces. Designed with an urban business hotel concept, it faithfully replicates the ambiance of a real hospitality setting. Printed steel panels with wood patterns enhance the space, adding warmth and sophistication. Commercial buildings like hotels are particularly well-suited for modular construction, as shorter build times enable earlier openings and faster revenue generation. Additionally, modular architecture is ideal for rapidly developing accommodations for global events such as the Olympics and international expos.
(1) High-Rise Modular Construction Technologies: H-Beam Modular Structural System
The second floor of H-Modular Lab serves as a testing and demonstration space for its applied technologies. The most notable feature is the H-Beam Modular Structural System, which forms the lab’s structural foundation. H-beams, one of the most widely used steel materials in construction, are valued for their high reliability, easy availability, and cost-effectiveness. Additionally, their open cross-section design facilitates efficient processing and seamless assembly on all surfaces.
In particular, the system optimizes the modular construction process by integrating a standardized framework and joint system, significantly improving efficiency. The standardized framework consists of modularized beam-column assemblies at the module’s corners, allowing for flexible module sizing by simply adjusting the length of the central H-beams. The standardized joint system features horizontal and vertical guides for precise positioning during stacking. With pre-installed bolts, modules can be accurately aligned and secured with minimal effort, streamlining on-site assembly.
(1) High-Rise Modular Construction Technologies: Steel Plate Shear Wall for Core Structures
The staircase leading to the second floor offers a clear view of the steel plate shear wall integrated into H-Modular Lab’s core structure. As the structural backbone of the building, the core enhances stability by reducing sway and torsion while resisting seismic and wind forces. It also serves as a vital functional hub, housing essential infrastructure such as elevators, staircases, electrical and mechanical rooms, and utility spaces—an indispensable component of any well-engineered building.
Traditionally, mid-to-high-rise modular buildings have relied on cast-in-place concrete cores, which are cost-effective and supported by extensive construction expertise. However, this method has a key limitation: no other work can proceed on-site while the concrete is being poured. To overcome this constraint and fully leverage the time-saving advantages of modular construction, Hyundai Engineering and Hyundai Steel are developing a dry steel core system as an alternative to conventional concrete cores in mid-to-high-rise modular buildings.
The steel plate shear wall in the core section is constructed by fitting steel plates into a rectangular frame, providing exceptional strength and rigidity against lateral forces such as wind and, most notably, seismic loads due to its high ductility. Unlike traditional concrete walls, it is lighter and can be prefabricated in a factory for modular on-site assembly, significantly accelerating the construction process.
(1) High-Rise Modular Construction Technologies: Hybrid Fireproofing Method
Efforts to enhance the safety of high-rise modular buildings also extend to fireproof construction, which ensures structural integrity for an extended period in the event of a fire. This system is designed to delay building collapse, protecting lives and property, making it essential for high-rise structures. In South Korea, buildings over 13 stories must meet a fire resistance requirement of at least three hours.
At H-Modular Lab, a hybrid fireproofing method is being tested that combines fire-resistant boards and fireproof coatings to minimize overall layer thickness. This method ensures sustained heat resistance even if the fire-resistant board deteriorates, as the coating expands upon heat exposure to form an insulating barrier. By maintaining structural fire safety while reducing the thickness of protective layers around columns and beams, this approach maximizes interior space. Researchers at H-Modular Lab are actively exploring various techniques to determine the optimal hybrid fireproofing solution.
(2) Technologies for Fast and Precise Modular Construction: PC Floor Slab
In modular construction, complex corridor layouts between modular units and the core require precise management of multi-directional construction tolerances. At H-Modular Lab, various technologies are being tested to address these challenges, including the integration of *PC slabs to enhance constructability while maintaining safety and quality, as well as advanced joint systems for seamless connections between the core and corridor slabs.
*Precast Concrete slab: A construction method in which floor slabs are cast and cured in a factory before being assembled on-site.
(2) Technologies for Fast and Precise Modular Construction: Bathroom POD
A Bathroom POD is a modular system that constructs an entire bathroom as a single unit, enabling fast and efficient installation. Conventional bathroom construction involves multiple complex steps, including waterproof thresholds, masonry, waterproofing, protective mortar, tiling, and sanitary fixture installation. By prefabricating these components in a factory setting, this system significantly reduces construction timelines while enhancing labor efficiency and quality control. Constructed on waterproof panels made from the same material as bathtubs, it eliminates leakage concerns. Additionally, the integration of a *raised floor plumbing system helps minimize inter-floor noise, making it particularly advantageous for residential buildings.
*Raised Floor Plumbing System: A plumbing installation method where pipes are embedded within an insulated floor layer or wall to prevent noise transmission to the lower floors.
(3) Innovative Technologies for Enhanced Living: Fireproof Door Frames for Steel Modular Structures
To enhance the quality and residential comfort of modular construction, Hyundai Engineering has incorporated advanced technologies into H-Modular Lab. A prime example of this meticulous refinement is the fireproof door frame for steel modular structures. In conventional modular construction, standard fireproof door frames are installed by welding reinforcement components directly onto the adjacent steel framework.
In H-Modular Lab, the dedicated fireproof door frame is secured to the front of the steel structure using a flange, a specialized fastening component. In steel modular structures, airtight and moisture-resistant membranes are commonly applied to form a sealed layer. The integration of a flange has streamlined the process of securing these membranes, further enhancing overall airtight performance.
(3) Innovative Technologies for Enhanced Living: Reducing Inter-Floor Noise by Utilizing Ceiling Space
Inter-floor noise remains a critical challenge even in modular construction. To address this, H-Modular Lab has been designed to allow for independent testing and replacement of the first-floor module ceiling and the second-floor module floor to evaluate floor impact noise performance. In modular structures, boards are affixed to the roof to facilitate assembly and protect interior finishes during transport, naturally creating an air cavity. Hyundai Engineering is actively developing a solution that utilizes this space by incorporating 'resonator-type sound-absorbing materials,' effectively reducing inter-floor noise without compromising ceiling height.
As part of H-Modular Lab’s development, Hyundai Engineering designed the first-floor ceiling to be removable and replaceable, allowing for structured testing and validation of various technologies. Furthermore, the company aims to enhance inter-floor noise mitigation by optimizing both ceiling cavities and floor structures.
Since 2012, Hyundai Engineering has been conducting research and development in modular construction technology as part of its efforts to revolutionize construction production methods and drive advancements in architectural innovation. Through collaboration with various external institutions and active participation in multiple national OSC (Off-Site Construction) R&D projects, the company has amassed extensive expertise in the modular construction field. This expertise is exemplified by the completion of Korea’s tallest modular residential building, the 13-story Gyeonggi Happy Housing in Yongin Yeongdeok.
Modular construction has become a core architectural technology and a defining trend in the industry. Hyundai Engineering and Hyundai Steel are committed to reshaping the industry paradigm with world-class modular construction technology. By leveraging the strengths of both the construction and manufacturing sectors, they seek to address labor shortages, enhance safety, and promote sustainable building practices—ultimately driving ESG-focused innovation. As such, H-Modular Lab is more than just a technological testbed; it represents Hyundai Engineering and Hyundai Steel’s vision and dedication to modular housing, paving the way for a better future.
Photography by Cho Hyuk-soo