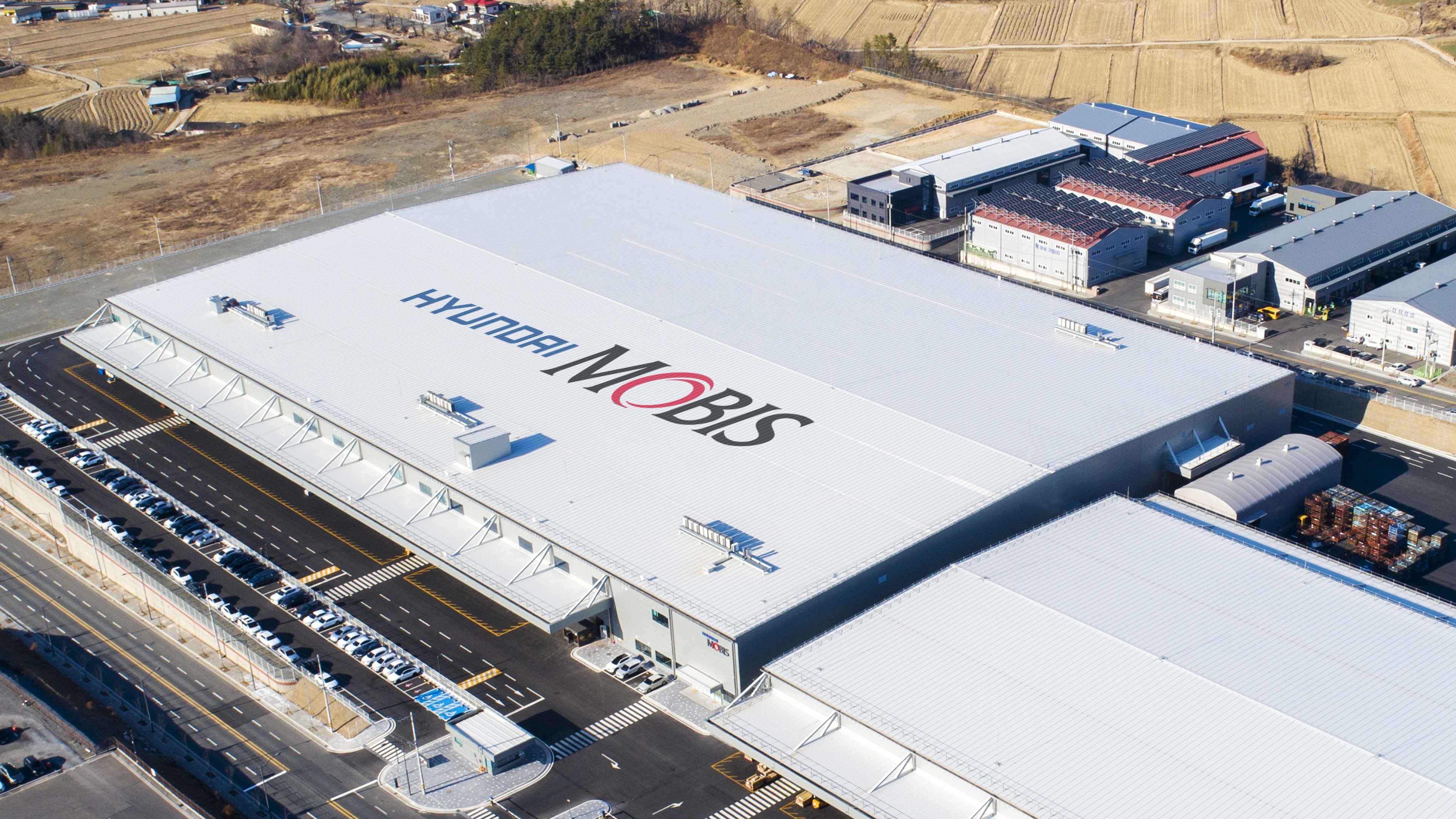
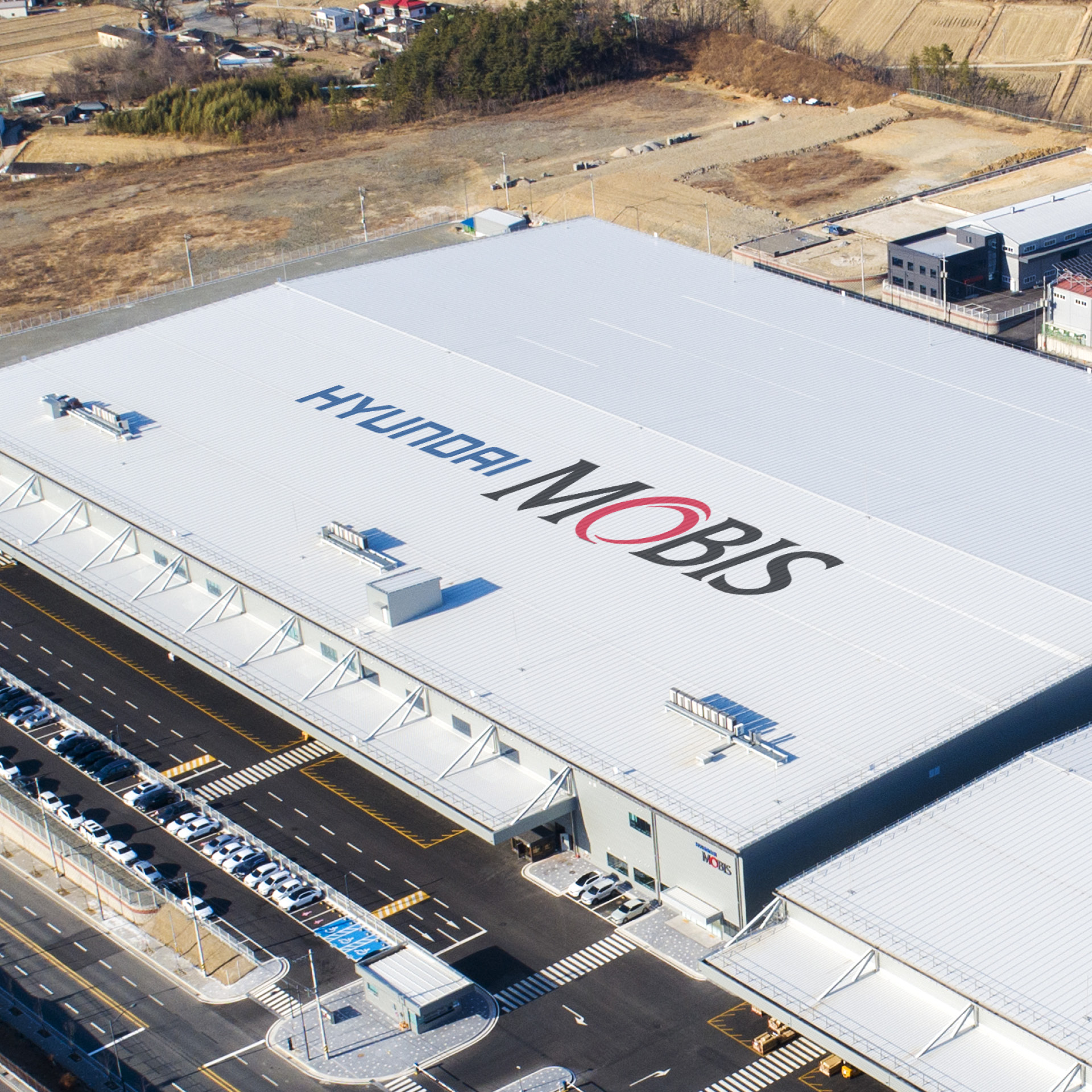
2025.07.01 Hyundai MOBIS
Cars demand continuous care to perform at their best. Timely replacement of consumables is key to maintaining performance and safety, which is why easy and fast access to A/S parts is so important. When those parts are hard to source, the burden of ownership increases significantly.
A/S parts are in a different league compared to everyday consumer products. While shoppers can choose between countless options based on personal preference when buying a phone case or a pair of sneakers, A/S parts are essential, non-negotiable components required for vehicle repairs. If a specific part isn’t available, the repair simply can’t happen. That’s especially critical in service bays, where multiple parts often need to come together at once. Any hiccup in the supply chain can derail the entire repair schedule, leading to delays and downtime for both shops and customers.
That’s why Hyundai Mobis, the exclusive supplier of Hyundai and Kia A/S parts, has invested heavily in a tightly integrated global logistics, distribution, and system infrastructure. The goal? To get the right parts to the right place, fast. Their efforts have earned Hyundai and Kia a reputation among customers as brands whose parts are available practically anywhere in the world. But Hyundai Mobis isn’t resting on its laurels. It’s pushing ahead with a full-scale transformation of the A/S supply chain.
In May, Hyundai Mobis opened a second large-scale logistics hub in Korea—the Yeongnam Logistics Center, located in Gyeongju, North Gyeongsang Province. This new facility significantly boosts the speed and stability of A/S part deliveries, ensuring that Hyundai and Kia owners across the country can access timely repair service when they need it most.
Replacing and consolidating three former regional facilities (in Oedong, Naengcheon, and Gyeongsan), the Yeongnam Logistics Center now serves as the unified hub for the entire region. The site spans 81,000 square meters—roughly the size of 11 soccer fields—and manages 175,000 different A/S parts for 152 Hyundai and Kia models.
This center serves exclusively domestic A/S parts needs, receiving components from 270 regional suppliers. Here's how the supply process works: parts produced at Hyundai and Kia plants, Hyundai Mobis factories, and by partner vendors are first delivered to logistics centers like Yeongnam. From there, they're distributed to 24 regional parts depots, which in turn supply 40 vehicle maintenance teams and more than 1,000 authorized parts dealers across Korea.
To manage this enormous supply chain, Hyundai Mobis utilizes a unified logistics system that tracks every detail—from part intake and inventory to delivery and restocking. If inventory falls below a set threshold, the system can automatically trigger restock procedures or a-lert staff for immediate action. This preemptive system helps avoid costly delays due to part shortages.
With Yeongnam now joining the existing Asan Logistics Center, Hyundai Mobis has secured two massive domestic logistics hubs. Together, they provide a powerful backbone for national A/S parts distribution, especially in production-heavy regions like Yeongnam and Chungcheong. Senior manager Mun-ki Baek, head of the Yeongnam Logistics Center, explains the vision behind it:
“The Yeongnam Logistics Center consolidates our three previous sites in Gyeongju, Gyeongsan, and Naengcheon into one large-scale logistics hub. By bringing everything under one roof, we’ve made it easier for our partner suppliers to deliver efficiently, and we’ve significantly improved operational logistics to provide better service for our customers.”
Things move fast at Hyundai Mobis’s Yeongnam Logistics Center—and they mean fast. From 8 a.m. to 5 p.m. daily, over 150 trucks roll through the gates non-stop. That’s parts coming in from more than 270 suppliers and heading right back out to service centers across the country. The order volume? A jaw-dropping 14,000 in-and-out transactions per day. This isn’t a warehouse—it’s a high-octane supply machine. And to keep that machine running smoothly, Hyundai Mobis didn’t just upgrade—they went full automation. From intake to shelving to outbound fulfillment, the entire flow is hands-free and lightning-fast. For smaller components, the facility runs an automated storage system that can handle over 21,000 custom bins, each zipping in and out of robotic cells with precision.
So what happens when you automate an entire parts logistics operation? According to senior manager Mun-ki Baek, the results are clear: not only does it reduce the physical burden on workers, but it dramatically boosts overall efficiency:
“The automated warehouse cuts down on manual labor and ramps up efficiency at the same time,” explains senior manager Mun-ki Baek. “In the past, when parts came in, workers had to sort and store everything by hand. And when it was time to ship, they’d push carts through the aisles to pick the orders—very labor-intensive, with a lot of wasted movement. Now, the system takes care of all that. The bins go in and out automatically, no walking required. It’s simple to use, too—just scan the part’s barcode, load it into the bin, and the system finds an open spot for storage. When it's time to ship, the right bin shows up on its own. You just check the quantity and pull the part. Thanks to this setup, we’ve doubled—sometimes even tripled—our hourly processing rate compared to the old manual method.”
Backed by this high-speed logistics system, the Yeongnam Logistics Center can ship auto parts to regional depots almost instantly. And for those rare moments when a part is urgently needed outside the region—say, when a service center across the country needs something that’s only in stock at Yeongnam—Hyundai Mobis has that covered too. Their emergency relay system ensures next-morning delivery by routing parts through strategically placed transfer hubs. It’s all about minimizing downtime and keeping customers on the road.
Yeongnam is also setting the pace when it comes to sustainability. The facility’s entire 36,300-square-meter rooftop is covered in solar panels. It’s part of Hyundai Mobis’s commitment to the global RE100 initiative, which aims to power all domestic and international operations with 100% renewable energy by 2040. For them, green energy isn’t a buzzword—it’s baked into the foundation of every new logistics hub they build.
Hyundai Mobis oversees a staggering inventory of OEM parts—2.8 million unique components across 205 vehicle models—making it one of the most complex automotive supply networks in the world. To manage this massive operation, the company has built out 54 logistics hubs worldwide, covering North America, Europe, China, and Asia. In Korea, it operates the Asan Logistics Center, which handles both domestic and export parts, and the Ulsan Center, which focuses exclusively on exports. With the recent addition of the Yeongnam Logistics Center, Korea’s nationwide parts supply system just got a whole lot stronger.
Hyundai Mobis isn’t just building warehouses—it’s fine-tuning an entire logistics ecosystem. According to senior manager Mun-ki Baek, who leads the Yeongnam hub:
“We’re working to improve logistics efficiency at every stage of the delivery process. Even with the exact same part, a smarter supply chain means the customer receives it faster—and that makes all the difference. That’s why we’re constantly asking ourselves: how do we operate each hub to move quicker, deliver smoother, and serve better? Getting the right part to the right place as fast as possible—that’s the job.”
A reliable flow of auto parts isn’t just a back-end operation—it’s a direct driver of brand trust and customer satisfaction. That’s why Hyundai Mobis is going all-in on smarter logistics, network expansion, and supply chain innovation. With every upgrade, they’re raising the bar for what customers can expect—faster repairs, smoother service, and confidence that their Hyundai or Kia is always in good hands.